Методика внедрения инструмента бережливого производства 5S
Библиографическое описание:
Васильева, С. Е. Методика внедрения инструмента бережливого производства 5S / С. Е. Васильева, С. Ю. Данилова. — Текст : непосредственный // Молодой ученый. — 2016. — № 13 (117). — С. 388-393. — URL: https://moluch.ru/archive/117/31280/ (дата обращения: 07.08.2020).
Ключевой целью системы 5S является создание организованного и чистого рабочего места, которое предусматривает безопасное и стабильное кружение, более лёгкое определение потерь и отклонений [1].
Предлагаемая методика 5S основана на пятиуровневой последовательности (таблица 1).
Таблица 1
Описание системы 5S
Уровень | Название | Описание |
1 | Сортировка | Хранение исключительно необходимого |
2 | Создание порядка | Свое место для каждой вещи и каждая вещь на своем месте |
3 | Соблюдение чистоты | Приведение зоны к первоначальному виду и поддержание аккуратного рабочего места |
4 | Стандартизация | Стандарты, кто что и когда делает во всех зонах |
5 | Совершенствование | Поддержание системы и измерение ее эффективности |
Рассмотрим каждый уровень более подробно.
Уровень 1. 1S. Сортировка
Сортировка — это хранение только того, что необходимо для создания ценности для клиента, когда ничего больше нельзя убрать. Необходимые на рабочем месте предметы отделены от ненужных предметов, которые затем удаляются. Это относится не только к дополнительным материалам (например, инструменты, оборудование, стеллажи), но и к прямым материалам. Для прямых материалов требуется установить максимальные и минимальные уровни всех запасов. Минимальный уровень устанавливается на основе Клиентского спроса при сохранении стабильного производства. Максимальный уровень запасов — это минимальное количество, необходимое для поддержания стабильного производства и, соответственно, поддержания нетерпимости к потерям. Сортировка тесно связана с Принципами управления материалами на предприятии. Она требует хорошего баланса рабочей нагрузки смежных процессов, которые стандартизированы таким образом, что производство является стабильным. Сортировка — один из самых важных инструментов предприятия для достижения уровня 3 ключевых концепций предприятия.
Уровень 2. 2S. Создание порядка
На этом уровне определяется место для каждого необходимого предмета и расположение этих предметов в зоне, так что в основном у всего есть своё место, и всё находится на своих местах. Кроме того, в качестве ключевого элемента этого уровня, важно выявление источников загрязнения и устранение основных причин этого для обеспечения требуемых условий и избежания нежелательных элементов или нежелательных ситуаций.
Уровень 3. 3S. Соблюдение чистоты
На этом уровне наступает необходимость генеральной уборки, приведения зоны в первоначальное состояние, а также поддержание аккуратного рабочего места. Она начинается с полной очистки и приведения всех элементов в зоне к начальным условиям, а затем устанавливается график уборки для поддержания стандартов и выявления отклонений от нормы. Подметание полов, вытирание машин, покраска обеспечивают приведение всего на заводе в чистый вид. Чистка позволяет увидеть повреждения, такие как трещины, протечки и износ; и предвидеть будущие поломки. Очистка скребком должна проводиться на регулярной основе. Выделите определенное время для уборки (например, последние пять минут смены). Определите, что надо чистить, а затем распределите задачи между конкретными людьми. Необходимый уборочный инвентарь и расходные материалы должны быть доступны в точке использования.
Уровень 4. 4S. Стандартизация
Стандартизация — это включение практик первых трёх S в ежедневную работу, это определение стандарта, кто, что, когда и как делает на всех участках. Стандарты 5S для всех зон завода устанавливаются и поддерживаются с помощью визуальных изображений стандартного состояния. Для поддержания хорошего состояния 5S каждый должен знать, что он несёт ответственность за выполнение, а также что, почему, когда, где и как делать.
Ниже на рисунке 1 представлены ключевые факторы успеха от внедрения системы 5S. На рисунке 2 представим более подробно последовательность операций процесса на примере предприятия по производству автокомпонентов.
Рис. 1. Развернутое описание ключевых факторов успеха
Рис. 2. Последовательность операций процесса
Уровень 5. 5S. Совершенствование
На этой фазе целью является поддержание системы 5S и создание системы оценки для обеспечения эффективности. Обеспечьте дисциплинированное соблюдение правил и процедур 5S для предотвращения нарушений. Придерживайтесь правил для поддержания стандарта и продолжайте совершенствоваться каждый день.
В результате предложенное мероприятие позволит:
– 5S тесно связана с безопасностью труда
– Рабочая среда влияет на вовлеченность сотрудников
– На чистом и организованном предприятии легче определить потери
– 5S влияет на восприятие нас клиентами и инвесторами
– 5S и наглядное управление предусматривают безопасную и стабильную среду, более легкое определение потерь и ненормальных состояний [2].
После внедрения процедуры 5S необходимо разработать оценочный лист (таблица 2) и один раз в месяц оценивать уровень применения данной процедуры.
Таблица 2
Оценочный лист по 5S апримере предприятия по производству автокомпонентов
5S | AREA | Участок | 1 | Очень плохо — Нет контроля | |||||||
AUDITED BY | 5S | 2 | Плохо — Некоторый контроль | ||||||||
Date | 12.02.2014 | 3 | Ср уровень — Частично под контролем | ||||||||
Пошив | 4 | Хорошо — Приемлемо | |||||||||
5 | Очень хорошо- Под контролем | ||||||||||
5S | No | Чек лист | Описание | 1 | 2 | 3 | 4 | 5 | Comments | ||
Seiri Separate Селекция | 1 | Все машины и части оборудования постоянно используются | Нужно нам или нет? Ненужные отметить красной лэйблом 5S. | 5 | |||||||
2 | Нет посторонних предметов на рабочих площадях | Нужно нам или нет? Проверить. Ненужные отметить красной лэйблом 5S. | 5 | ||||||||
3 | Все ненужные части четко обозначены | Все ненужные предметы (помеченные красной лэйблом 5S) убраны | 5 | ||||||||
4 | Все контейнеры, рабочие области, стеллажи и инструменты четко обозначены | Проверить | 5 | ||||||||
25 | 5 | Доски отчетов обновлены и хорошо представлены | Все графики и отчеты действительны и презентабельны | 5 | |||||||
Seiton Straighten Сортировка | 6 | Все площади четко обозначены? | Все участки и материалы четко обозначены? | 5 | |||||||
7 | Все документы и файлы промаркированы и аккуратно размещены | Документы и файлы промаркированы и правильно размещены | 5 | ||||||||
8 | Места хранения на рабочих местах и рабочие места разработаны с целью простоты использования | Все расположено в пределах вытянутой руки | 5 | ||||||||
9 | Весь запас храниться в спец месте | Места для всего и все на своих четко обозначенных местах | 4 | Не укрыты часть стеллажей банка кроя | |||||||
24 | 10 | Зоны досок контроля чистые и проход к ним не затруднен | Нет загромождений в проходах к доскам контроля | 5 | |||||||
Seiso Scrub Уборка | 11 | Проверяемая площадь всегда чистая и свободная от лишних предметов | Стараться удалить грязь повторно не повредит | 5 | |||||||
12 | Машины чистые? | Все машины очищены от грязи пыли и масла | 5 | ||||||||
13 | Действует система по уборке (часть ODS) — отображена и актуальна | Операторы поддерживают чистоту в течение смены | 5 | ||||||||
14 | Нет кабелей, проводки, воздухоотводов, лежащих на полу или плохо закрепленных | Всё закрепляется четко на месте | 5 | ||||||||
25 | 15 | Уборочное оборудование | Хранение оборудования рядом с рабочей зоной | 5 | |||||||
Seiketsu Standardise Стандартизация | 16 | Показаны основные процедуры и стандартные операции отображены | Четко видны и актуальны | 5 | |||||||
17 | Операторы прошли тренинг и знают 5S | Операторы знают 5S | 5 | ||||||||
18 | Показать стандарты 5S | Стандарты 5S показаны | 5 | ||||||||
19 | Аудиты 5S регулярны и результаты представлены | Проверить отчет по аудитам | 5 | ||||||||
25 | 20 | Вывоз отходов | Есть мусорные ведра и они регулярно опустошаются | 5 | |||||||
Shitsuke Sytemise Систематизация | 21 | Спецодежда | Все операторы носят спецодежду и защитные приспособления | 5 | |||||||
22 | Ознакомление с 5S и ОТиТБ | Все операторы ознакомлены с 5S и требованиями ОТиТБ | 5 | ||||||||
23 | Мастерские 5S в случае необходимости | Проверять отчеты 5S после каждого изменения layout или запуска новой модели/проекта | 5 | ||||||||
24 | Все ознакомлены с планом эвакуации, техникой безопасности и сборки | Спросить оператор о местоположении | 5 | ||||||||
25 | 25 | Информация по качеству представлена для мотивации персонала (IPPM и т. д.) | Данные показаны и операторы ознакомлены? | 5 | |||||||
Необходимые условия для успешной реализации процедуры:
Определенное лидерство по предприятию, выполнение обходов 5S
– Ресурсы, определенные по участкам
– Выбор показательной области для создания концепции, которая может использоваться для
– распространения на остальную часть предприятия
– Выполнение перекрёстных проверок и закрытие вопросов
– Выполнение графика уборки
– Видение будущего состояния и чёткий план действий по его достижению
Таким образом, предложенная методика позволит эффективно организовать рабочее место.
Литература:
- Агеева И. М., Данилова С. Ю. Оптимизация производственного процесса за счет внедрения инструментов бережливого производства 5S / И. М. Агеева, С.Ю, Данилова // «Современные подходы к трансформации концепций государственного регулирования и управления в социально-экономических системах»Материалы 2-й Международной научно-практической конференции Курск, 19 февраля 2013 г. в 2-х томах: Изд-во ЗАО «Университетская книга, 2013. — Ч.1. — С. — 25–31.
- Степина, С. Е., Чернова Д. В. Методика анализа логистических процессов автосервисного предприятия в рамках концепции бережливого производства / С. Е. Степина, Д. В. Чернова // Вестник Самарского государственного экономического университета. — 2011. С.100–106.
- Womack, J. Seeing the Whole: Mapping the Extended Value Stream [Text] / J. Womack, D. Jones. — Brookline: Lean Enterprise Institute, 2002. — 152 р.
Основные термины (генерируются автоматически): место, уровень, AREA, AUDITED, IPPM, ODS, аккуратное рабочее место, оценочный лист, рабочее место, стабильное производство.
Принципы и инструменты бережливого производства системы 5S
Система 5S – один из ключевых инструментов бережливого производства, направленный на повышение безопасности, эффективности и производительности труда на рабочем месте (рабочем пространстве). Благодаря своей простоте и эффективности часто является начальным этапом совершенствования производственной системы. При этом реализация данной методики формирует новую культуру производства, позволяющую качественно изменить организацию.
Название метода происходит от 5 шагов, каждый из которых начинается на “С”. Так как систему придумали в Японии, оригинальные названия читаются примерно так: Seiri, Seiton, Seiso, Seiketsu, Shitsuke. Позже 5 этапов внедрения были переведены на английский: Sort, Straighten, Sweep, Standardize, Self-discipline, – и русский. Один из вариантов русского перевода: Сортировка, Самоорганизация, Сияние, Стандартизация, Совершенствование. Из-за наличия русского перевода этапов название системы можно встретить как в латыни (5S), так и русскоязычном варианте (5С).
Примечателен тот факт, что схожая система – CANDO (Clearing, Arrangement, Neatness, Discipline, Organization), – появившаяся в США намного раньше, чем 5S, в наши дни менее известна и распространена. По некоторым источникам, CANDO – один из тех принципов бережливого производства, которые основатель производственной системы Toyota позаимствовал во время визита на завод Ford.
Первый шаг системы 5S – Сортировка
На данном этапе все мероприятия сводятся к определению необходимых для работы инструментов и удалению всех ненужных, неисправных или неиспользуемых предметов. Для чего это делается? Для повышения безопасности на рабочем месте, стандартизации выполняемой работы – соответственно, повышения продуктивности и качества.
Практики бережливого производства называют этот шаг самым сложным, так как признавать ненужность предметов, которые долгое время находились под рукой, для большинства людей не так просто. В психологическом плане это требует отказа от привычного порядка, сформировавшегося за годы работы, и принятия нового, неизвестного, часто насаждаемого извне.
Для того, чтобы преодолеть сопротивление на этом этапе, чаще всего прибегают к трем приемам:
- Проводят обучение принципам бережливого производства и системы 5S.
- Вовлекают сотрудников в процесс реализации системы 5S на их непосредственных рабочих местах.
- Создают зону “красных меток” (Red Tag Area) – карантин для предметов, которые не используются на рабочем месте ежедневно, однако по тем или иным причинам не могут быть удалены немедленно.
Второй шаг системы 5S – Самоорганизация или систематизация
Как говорят практики бережливого производства: “всему свое место, и все на своих местах”. Данный этап нацелен на максимально рациональное размещение необходимых для работы предметов в рабочем пространстве. Чем чаще используется предмет, тем ближе и доступнее он должен быть расположен. Чем реже – тем больше шансов найти его за пределами рабочего места, например, в шкафу или на общем стенде.
Зачем это делается? Опять же, безопасность, продуктивность и качество. Удобно расположенный предмет обеспечит эргономику рабочего места и целевое применение. Те же инструменты, которые используются реже, следует разместить в поле общего доступа, что существенно сократит их необходимое количество.
Основные приемы данного этапа системы 5С – различные варианты визуализации: маркировка, зонирование, оконтуривание, метод “теней” и т.д.
Третий шаг системы 5S – Сияние или содержание в чистоте
Данный этап направлен на создание условий для поддержания чистоты рабочего пространства. Разумеется, это подразумевает уборку и чистку. Но на этом третий шаг внедрения системы 5С не завершается. Необходимо установить источники загрязнения – понять причины и разработать план мероприятий по их устранению.
Также на данном этапе разрабатываются графики и стандарты уборки (кто, как часто и чем проводит уборку?), а также обеспечивается необходимых для этих целей инвентарь.
Четвертый шаг системы 5S – Стандартизация
Стандартизация предполагает меры по закреплению и удержанию достигнутых результатов. Для этих целей разрабатываются организационные стандарты, которые в лаконичной и визуализированной форме закрепляют правила относительно обустройства, визуализации, уборки, зонирования и других параметров рабочих мест.
Кроме того, настоящий этап предусматривает создание системы контрольных механизмов, чаще всего аудитов 5С. Для чего это делается? Чтобы предотвратить постепенное “скатывание” системы к первоначальному состоянию.
Пятый шаг системы 5S – Совершенствование
Как проще всего обеспечить удержание полученных результатов? Только непрерывно совершенствуя рабочее пространство усилиями всех сотрудников: каждый сотрудник, каждый день, всюду!
На данном этапе применяют следующее:
- Обеспечивают информирование персонала о состоянии процесса развертывания системы 5S, результатах аудитов, выявленных проблемах и т.д.
- Обеспечивают интеграцию системы 5S и системы подачи предложений по улучшениям.
- Обеспечивают интеграцию системы аудитов 5S и премирования сотрудников.
5S | UMP
Система 5S одна из самых известных методик Бережливого производства. 5S считается «основополагающим» понятием системы LEAN, поскольку она определяет стабильность производимых операций, необходимую для создания и поддержки непрерывных усовершенствований.
5 составляющих системы 5S являются важными элементами в создании рабочей стабильности, необходимой для создания и поддержания процесса непрерывного улучшения, которым озадачены многие предприятия.
Главная цель заключается в создании чистой, упорядоченной и безопасной среды. Среды, где есть место для всего и все необходимое находится на своем месте.
Система 5S помогает сократить отходы, установить правила и дисциплину необходимые для поддержания и постоянного улучшения своего рабочего места. Многие компании начинают свою программу преобразования именно с 5S, потому что она достаточно быстро помогает устранить некоторые из видимых затрат, а также структурировать и упорядочить успешное следование другим инициативам непрерывного усовершенствования. Результы ее внедрения видны быстро
В основе системы лежат 5 принципов:
1. СОРТИРОВКА
Первый шаг системы 5S заключается в определении того, что необходимо сохранить и от чего избавиться. Ненужные предметы помечают «красной меткой». Это делается путем сортировки всех инструментов и материалов на рабочих местах и хранения исключительно предметов первой необходимости. Все остальное удаляют из рабочей зоны, чтобы освободить рабочее место от помех и опасностей.
Для организации процесса вы можете использовать:
- Ярлыки или бирки – Пометьте красным ярлыком неиспользуемые изделия и хранить их в определенном месте, чтобы сотрудники могли отсортировать и взять все, что по-прежнему необходимо. Любые предметы, не использовавшиеся в течение пяти дней, должны быть утилизированы.
- Ленты для маркировки пола — Для обозначения зоны с предметами, помеченными «красными ярлыками», в которой сотрудники могут найти то, что будет выброшено через несколько дней.
- Бланки протокола с красным ярлыком – Для отслеживания запасов, которые хранятся определенный срок и выбрасываются.
- Фотокамеру – Для того, чтобы делать фотографии данной зоны «до и после». Это очень наглядный инструмент при всей своей простоте — увидеть произошедшие изменения на фотографиях!
Лайфхак! Сортировать можно с использованием следующих принципов:
- нужные всегда — материалы, которые используются в работе в данный момент;
- нужные иногда — материалы, которые могут использоваться в работе, но в данный момент не востребованы;
- ненужные — брак, неиспользуемые инструменты, тара, посторонние предметы.
2. СОДЕРЖАНИЕ В ЧИСТОТЕ (СИСТЕМАТИЧЕСКАЯ УБОРКА)
Устраняя пыль, мусор, убирая источники загрязнения, проводя проверки оборудования вы повышаете уровень безопасности и производительность конкретного участка. Ваши рабочие места будут выглядеть как новые! И сотрудники будут с радостью приходить на работу. Каждый день…
Вы можете использовать:
- Чистящие средства и хозяйственный инвентарь – Включая веники, совки, салфетки, обезжиривающие и чистящие средства для мытья разных поверхностей.
- Щит для инструментов с контурами и маркировкой – Для хранения инвентаря.
- Средства индивидуальной защиты (СИЗ) – Включая перчатки и защитные очки, чтобы защитить сотрудников от опасных чистящих средств и мусора.
- Блокирующее оборудование – Для защиты работников от выпуска опасной энергии при выполнении очистки или технического обслуживания оборудования.
- Сорбенты в форме салфеток для периодической уборки и устранения проливов — Для повышения эффективности процесса и в случае сбора масляных и химических веществ.
Лайфхак! Соблюдение рабочего места в чистоте и опрятности. Порядок действий:
- разбить линию на зоны, создать схемы и карты с обозначением рабочих мест, мест расположения оборудования
- определить специальную группу, за которыми будет закреплена зона для уборки.
- определить время проведения уборки
3. СОБЛЮДЕНИЕ ПОРЯДКА
Пришло время найти способы сокращения источники отходов и ошибок на вашем объекте и сделать его визуально более наглядным. Легко? Не совсем. Стоит ли оно того? Определенно! Вы должны сосредоточиться на:
Организации оборудования:
Разработке мер безопасности:
- Знаки безопасности – Для информирования сотрудников о любых опасностях на рабочем месте.
- Маркеры для труб – Для немедленного уведомления вас о том, что вам нужно знать о содержании труб, направлениях потока и уровне безопасности.
Создании процедур:
- Этикетки с указанием процедуры — Разместить информацию о процедурах не в папках, а на полу цехов! Где их видят сотрудники и могут использовать ежедневно.
- Знаки безопасности – Разместить необходимую информацию по технике безопасности непосредственно в точке необходимости, что приводит к снижению затрат на профессиональную подготовку и повышению уровня безопасности.
Установление стандартов качества продукта:
- Ленты для маркировки пола – Для отметки полос движения, мест хранения, продуктов, которые должны быть проверены, для обеспечения качества и многое другое.
- Калибровочные этикетки – Для быстрого обнаружения отклонений в давлении или температуре с первого взгляда.
Создание эффективного учета и подъемно-транспортного оборудования:
- Магнитные этикетки для маркировки материалов – Для маркировки и организации пространства рабочих столов, полок, стеллажей, контейнеров, шкафов и транспортной тары.
- Показатели минимального и максимального уровней – Для определения ситуаций излишков запасов и точек, в которых запас должен быть заказан повторно.
Лайфхак! Четыре правила расположения вещей, которые позволяют их быстро найти и использовать:
- на видном месте;
- легко взять;
- легко использовать;
- легко вернуть на место
4. СТАНДАРТИЗАЦИЯ ПРОЦЕССА
Вы проделали хорошую работу, начав делать ваше рабочее место более бережливым. Теперь пришло время расширить свои усилия и создать практические приемы для сохранения данного стандарта компании. Это делается с помощью четких и последовательных функций и обязанностей, а также визуального контроля.
Вы можете использовать:
- Доску для планирования заданий – Визуализировать приказы о последовательности заказов и указать задержки по работы или пропущенные сроки.
- Графики и контрольные листы – Для показания того, какие сотрудники должны выполнять определенные задачи и когда эти задачи должны быть выполнены.
- Контрольная доска для отслеживания количества запасов – Контролировать использование запасов и обеспечить быстрое положение.
- Доски для оперативного бережливого менеджмента (УБМ) – Для отслеживания показателей и внедрения улучшений.
- Визуальные средства показания безопасного состояния – Как правило, для определения того, открыты или закрыты ли клапаны или воздушные насосы для предотвращения несчастных случаев.
5. СОВЕРШЕНСТВОВАНИЕ (ФОРМИРОВАНИЕ ПРИВЫЧКИ)
Не останавливайтесь сейчас! Вы сделали работу – теперь вам нужно сохранить ее результаты. Не останавливайтесь на достигнутом, дайте сотрудникам понять, что организация рабочего места является одним из главных приоритетов, и стремитесь к постоянному совершенствованию рабочего места.
Вы можете использовать:
- Свой собственный принтер, материалы для этикеток и программное обеспечение для создания этикеток – Создавайте знаки, ярлыки и ярлыки по мере необходимости.
- Графики линии поведения – Помогайте сотрудникам запомнить последовательности задач на основе стандартной диаграммы.
- Профилактические задачи технического обслуживания – Поддерживать предупредительные показания технического обслуживания в соответствии с маркировкой вибрации и точками ультразвукового датчика.
- Визуальные средства идентификации запасных частей – Для четкого определения правильных запасных частей.
- Уроки и этикетки, посвященные одному пункту – Помогайте сотрудникам помнить об иногда упускаемых или важных частях процедуры.
Что такое 5S? Система 5S. Система 5с
Что такое система 5S
Система 5S – это система организации рабочего места, которая позволяет значительно повысить эффективность и управляемость операционной зоны, улучшить корпоративную культуру, повысить производительность труда и сохранить время. Это первый шаг на пути к созданию бережливого предприятия и применению других инструментов системы менеджмента компании Toyota.
Краткая история системы 5S
В Японии системный подход к организации, наведению порядка и уборке рабочего места возник в послевоенный период, точнее, к середине 50-х годов ХХ века. В то время японские предприятия были вынуждены работать в условиях дефицита ресурсов. Поэтому они разработали для своего производства метод, при котором учитывалось все и не было места никаким потерям.
Первоначально в японской системе было только 4 действия. Слова, обозначающие эти действия, в японском языке начинаются с буквы «S»:
- Seiri (整理)– Sorting – сортировка.
- Seiton (整頓) – Straighten or Set in Order –рациональноерасположение.
- Seiso (清掃) – Sweeping – уборка.
- Seiketsu (清潔) – Standardizing – стандартизация работ.
Позже добавилось пятое действие, его назвали Shitsuke (躾) – Sustaining – поддержание достигнутого и совершенствование, и оно завершило цепочку элементов, которые теперь известны как 5S.
Сейчас система 5S обладает фундаментальной мощью для того, чтобы изменять рабочие места и вовлекать в процесс улучшений всех работников.
В систему 5s входят пять действий:
1) Сортировка – означает, что вы высвобождаете рабочее место от всего, что не понадобиться при выполнении текущих производственных операций.
Рабочие и руководители часто не имеют привычки избавляться от предметов, которые больше не нужны для работы, сохраняя их поблизости «на всякий пожарный случай». Обычно это приводит к недопустимому беспорядку или к созданию препятствий для перемещения в рабочей зоне. Удаление ненужных предметов и наведение порядка на рабочем месте улучшает культуру и безопасность труда. Чтобы более наглядно продемонстрировать, сколько лишнего скопилось на рабочем месте, можно на каждый предмет-кандидат на удаление из рабочей зоны повесить красный ярлык (флажок).
Все сотрудники вовлекаются в сортировку и выявление предметов, которые:
- должны быть немедленно вынесены, выброшены, утилизированы;
- должны быть перемещены в более подходящее место для хранения;
- должны быть оставлены и для них должны быть созданы и обозначены свои места.
Необходимо чётко обозначить «зону красных ярлыков» предметов с красными флажками и тщательно её контролировать. Предметы, остающиеся нетронутыми свыше 30 дней, подлежат переработке, продаже или удалению.
2) Рациональное расположение – означает определить и обозначить «дом» для каждого предмета, необходимого в рабочей зоне. Иначе, если, например, производство организовано по сменам, рабочие разных смен будут класть инструменты, документацию и комплектующие в разные места. В целях рационализации процессов и сокращения производственного цикла крайне важно всегда оставлять нужные предметы в одних и тех же отведённых для них местах. Это ключевое условие минимизации затрат времени на непродуктивные поиски.
3) Уборка (содержание в чистоте) – значит обеспечить оборудованию и рабочему месту опрятность, достаточную для проведения контроля, и постоянно поддерживать её.
Уборка в начале и/или в конце каждой смены обеспечивает немедленное определение потенциальных проблем, которые могут приостановить работу или даже привести к остановке всего участка, цеха или завода.
4) Стандартизация – это метод, при помощи которого можно добиться стабильности при выполнении процедур первых трех этапов 5S – значит разработать такой контрольный лист, который всем понятен и прост в использовании. Продумать необходимые стандарты чистоты оборудования и рабочих мест, и каждый в организации должен знать, как это важно для общего успеха.
5) Совершенствование – означает то, чтобы выполнение установленных процедур превратилось в привычку
Мероприятия, лежащие в основе 5S (сортировка, рациональное расположение, уборка, стандартизация и совершенствование), абсолютно логичны. Они представляют собой базовые правила управления любым продуктивно работающим отделом. Однако именно системный подход, который система 5S применяет к этим мероприятиям, и делает ее уникальной.
См. также:
Что такое 5S. Система 5S. Система 5с
Поделиться в соц. сетях
Бережливое производство и система 5S
Целью любого процесса является создание продукта от начала до конца процесса. Должны быть предприняты усилия для контроля потока, и если погрешности обнаружены, они должны быть немедленно устранены, когда знают бережливое производство, что это такое. Это происходит, когда процесс выходит за пределы своих возможностей. Важно, чтобы специалисты понимали процесс. Несоблюдение параметров процесса приведет к лишним расходам. Совершенство во всех процессах продукт является конечной целью. Бережливое производство подразумевает непрерывный безупречный поток продукции без отходов.
Основные инструменты системы бережливого производства:
- определение правильного тактового времени или темпа процесса;
- создание и использование системы для предотвращения появления отходов;
- использование устройств для обнаружения ошибок в процессе;
- создание четного потока или материала;
- стремление к совершенству.
Руководство ищет возможности улучшения в каждой части потока создания ценных изделий. Выявление и устранение основных причин проблем в производственных процессах для достижения совершенства. Бережливое производство исключает методы, которые не повышают ценность для клиентов. Принципы и концепции в области бережливого производства чрезвычайно полезны и обеспечивают глубокое понимание процесса бережливого производства. Бережливые производственные принципы являются ключевыми для работы. Устранить отходы производственного процесса довольно сложно, но это не невозможно. Многие руководители проектов на производственных объектах испытывают ту же борьбу, но считают экономичным производство жизнеспособным вариантом.
Внедрение бережливого производства подразумевает:
- определение участков, которые не считаются ценными для потребителя;
- исключение этих участков для снижения издержек производства.
Таким образом, можно постепенно разрешить производственной операции производить только то, что абсолютно необходимо, в конечном итоге избавляя фабрику от ненужного производства. В дальнейшем на продукцию потребуется получение разрешительных документов, таких как декларация таможенного союза или добровольный сертификат.
Система 5s бережливое производство.
Система 5s – комплексная методика улучшения производственного процесса путём оптимизации пяти связанных между собой этапов, собранная как цельная система в Японии в конце 20-го века. Наименование каждого из этапов в японском языке начинается на букву «s».
Но в русском языке на букву «с» подобраны соответствующие этим наименованиям аналоги, поэтому нередко в литературе используется адаптированное «русское» название метода бережливого производства – Система 5С, где:
- 1С – Сортируй – Seiri (Сейри).
- 2С – Соблюдай порядок – Seiton (Сейтон).
- 3С – Содержи в чистоте – Seisō (Сейсо).
- 4С – Стандартизируй – Seiketsu (Сейкецу).
- 5С – Совершенствуй (или Самодисциплина) – Shitsuke (Сицуке).
Существует адаптация и под английский язык, где наименование каждого этапа начинается уже на английскую букву «s»: Sorting, Set in Order, Sweeping, Standardizing, Sustaining the discipline.
Принципы бережливого производства.
1)Идентификация ценности — определение ценности клиента является наиболее важным аспектом бережливого производства. Определение ценности может быть чем-то, что потребитель считает абсолютно необходимым.
2) Сопоставление потока создания ценности. После определения значения настало время перейти к сопоставлению потока создания ценности. Этот процесс включает в себя определение каждого аспекта процесса, с самого начала, где собирается сырье, до доставки продукта. Этот принцип помогает найти другие этапы производства отходов, что в конечном итоге позволяет операции разработать план по его устранению. Создание потока — после того, как принят план для устранения отходов.
3) Следующим шагом является наблюдение за оставшимися действиями в рамках операции. Это делается для того, чтобы в процессе не было проблемных мест, прерываний или любых других проблем.
После того, как недочеты внутри процесса выяснены, производственный поток становится намного быстрее и эффективнее. Это связано с устранением бесценных шагов. Это позволяет потребителям извлечь продукты по мере необходимости. Для реализации продукции на торгах организации потребуется сертификат РПО или сертификат деловой репутации.
В поисках совершенства — внедрение этих шагов само по себе значительно улучшит производственные мощности, но бережливое производство требует значительных усилий и изменения мышления. Вместо того, чтобы рассматривать это как просто метод производства, важно рассматривать его как культуру, требующую нахождения всех специалистов на рабочих местах. Несколько раз пройдя процесс по методологии бережливого производства, можно приблизиться к полной реализации своего производственного объекта. Наряду с бережливыми принципами, надо знать об общих отходах в процессе производства.
Система 5С в бережливом производстве
Содержание системы 5С
Определение 1
Система 5S (5С) – метод организации рабочего места (пространства), нацеленный на создание оптимальных условий труда, поддержания порядка и чистоты.
Системы 5С является инструментом бережливого производства, японским методом организации труда. Поддержание порядка в рабочем пространстве позволяет сотрудникам экономить место, время и энергию на поиск необходимых для работы предметов. Содержание рабочего места в порядке способствует повышению эффективности труда.
Поддержание порядка на рабочем месте важно как для производственных рабочих, так и для сотрудников умственного труда (офисных работников). Чистота и аккуратность способствуют эффективной организации рабочего процесса, которая, в свою очередь, лежит в основе качества производимых продуктов или предоставляемых услуг и соответствия требованиям результативности процессов труда.
Система 5C представляет собой пять шагов по наведению порядка в рабочем пространстве.
Шаги метода 5С
- SEIRI (Сортировка) – этот шаг представляет собой удаление с рабочего места ненужных предметов. Для этого необходимо разделить все предметы в рабочем пространстве на те, которые необходимо удалить (утилизировать, выбросить), перенести в место хранения или оставить для выполнения работы. Сортировка предполагает установление единых правил для определения категории каждого предмета на рабочем месте.
- SEITON (Самоорганизация) – определение места для каждой необходимой вещи. Каждый сотрудник на своем рабочем месте должен расположить все оставшиеся предметы таким образом, чтобы их использование способствовало повышению эффективности рабочего процесса, они должны быть легко доступны для всех, кому они могут понадобиться. Для обеспечения более быстрого поиска предметы маркируются.
- SEISO (Соблюдение чистоты) – систематическая уборка рабочего места. С целью соблюдения чистоты необходимо создать такую систему, которая не загрязняется – разграничить рабочие зоны и обозначить границы, осуществлять регулярную уборку рабочих мест и оборудования.
- SEIKETSU (Стандартизация) – обеспечение регулярности выполнения первых трех шагов. В рамках реализации первых шагов должны быть найдены некоторые эффективные решения, которые следует закрепить документально или письменно, чтобы сделать их более запоминающимися для сотрудников. Стандартизация предполагает разработку стандартов действий по наведению порядка на рабочем месте с применением визуального контроля.
- SHITSUKE (Совершенствование порядка и дисциплина) – поддержание рабочего пространства в порядке в соответствии с разработанными и принятыми стандартами. На этом этапе происходит признание системы 5С как части рутинной деятельности сотрудников компании и начинается процесс ее совершенствования, улучшения – сотрудники могут самостоятельно предлагать изменения в существующие стандарты действий по наведению порядка и внедрять новые улучшенные решения.
Готовые работы на аналогичную тему
Преимущества системы 5С
Система 5С представляет собой метод конструирования, организации и стандартизации рабочего пространства. Структурирование условий работы позволяет сделать труд сотрудников более легким и концентрированным, а также повышает мотивацию. Система 5С позволяет сотрудникам идентифицировать себя с рабочей системой.
Система 5С улучшает безопасность условий труда сотрудников, так как все средства производства и предметы, используемые в процессе труда, упорядочены и занимают строго определенное место.
Система 5С позволяет организовать рабочее место и рабочую систему таким образом, чтобы сократить потребности сотрудников в необходимых предметах, а также установить место и количество необходимых предметов.
5S — система бережливого производства
Система 5S как первый шаг внедрения бережливого производства на промышленном предприятииВ последнее время всё большую популярность приобретает бережливое производство. Для его внедрения требуется трансформация менталитета работников и руководителей предприятий, которые обязаны научиться выявлять потери, понимать, какие действия или состояния реально являются потерями, и непрерывно работать над их устранением. Начать внедрение бережливого производства можно с системы организации рабочего пространства 5S («Упорядочивание»), разработанной на рубеже 60-70 гг. ХХ века в Японии.
Система 5S включает в себя пять шагов (табл. 1) [1; 4].
Таблица 1 — Суть этапов системы 5S и возможные эффекты
Наименование этапа | Расшифровка | Виды эффектов: П – производительность; Б – Безопасность; К — качество |
1. Удаление ненужного | Все предметы рабочей среды разделяются на три категории: нужные, ненужные и не нужные срочно. Ненужные удаляются по определенным правилам. Нужные сохраняются на рабочем месте. Не нужные срочно располагаются на определенном удалении от рабочего места или хранятся централизованно. Распределяются и закрепляются зоны ответственности каждого работника | П: Сокращение ненужных запасов Сокращение занимаемых площадей Б: Сокращение травматизма за счет освобождения производственной среды от ненужного К: Улучшение сохранности сырья, материалов, готовой продукции |
2. Упорядочение размещения предметов | По отношению к нужным предметам и предметам, не нужным срочно, вырабатываются и реализуются решения, которые обеспечивают: — быстроту, легкость и безопасность доступа к ним; — визуализацию способа хранения и контроля наличия, отсутствия или местонахождения нужного предмета; — свободу перемещения и эстетичность производственной среды | П: Эффективное использование рабочих мест, улучшение организации труда. Сокращение потерь времени на поиски, хождения и т.п. Б: Сокращение травматизма из-за безопасного способа хранения предметов – создание безопасной ситуации К: Сокращение брака из-за случайного использования несоответствующих компонентов |
3. Очистка рабочего места | Определяются основные источники загрязнения рабочего пространства. Проводится анализ и определяется, кто имеет доступ к документам /деталям, к каким именно, каким образом и т.д. | П: Сокращение простоев из-за неисправности оборудования Б: Улучшение санитарно-гигиенических условий труда. Предотвращение утечек пара, газа, воздуха, воды и опасных веществ. Сокращение аварий из-за неисправности оборудования. Устранение причин аварий, пожаров, несчастных случаев К: Сокращение брака и потерь, связанных с загрязнением. Сокращение брака из-за неисправности оборудования и контрольно-измерительных приборов |
4. Стандартизация правил уборки | Разрабатывается инструкция, включающая правила пользования документами/деталями в отделах /на участках. Определяется круг лиц, которые имеют право ими пользоваться | П: Сокращение потерь за счет визуализации контроля и управления Б: Визуализация контроля безопасности К: Стандартизация методов контроля |
5. Формирование привычки соблюдать чистоту и порядок | Разработанные на 4-м этапе инструкции утверждаются приказом директора, изданным по предприятию. С людьми, занимающими должности, которые имеют доступ к документам/деталям, проводится инструктаж по работе. По окончанию инструктажа, подписывается документ, подтверждающий, что человек с инструктажем ознакомлен. Обязательно назначается лицо, ответственное за хранение документов / деталей. При необходимости вводится система штрафов | П: Рост выработки за счет мотивированности персонала на производительный труд Б: Соблюдение правил охраны труда. Безопасное производственное поведение К: Сокращение брака из-за невнимательности или недисциплинированности персонала |
Внедрение системы 5S является первым шагом к развёртыванию бережливого производства (Lean-Manufacturing) и воспитания в персонале способности осуществлять постоянное совершенствование производственной среды и поддерживать достигнутый уровень. Для повышения эффективности внедрения 5S на промышленном предприятии следует вводить конкурсы «Лучный цех», «Самый чистый рабочий участок» и т.д. Одновременно следует присваивать звание «Худший цех» и «Самое грязное рабочее место» для повышения дисциплины.
В ходе проведения 5S – упорядочения, провидится инвентаризация специализированной оснастки и составляется перечень не задействованного спец. инструмента. По её итогам должно быть списано и отправлено на дальнейшую утилизацию изношенных и снятых с производства агрегатов, оборудования, металлического лома. Сумма, полученная с утилизации и переработки и будет суммой прямого экономического эффекта.
Однако, эффект от данных мероприятий заключается не только в снижении затрат на производство, увеличения цены выпускаемой продукции за счёт роста качества, снижении затрат времени на изготовление единицы продукции, но и в психологической составляющей – работники будут с большим энтузиазмом и эффективностью работать на аккуратном, чистом рабочем месте (табл. 1).
Основным результатом является относительная экономия ресурсов, а не затрат, в первую очередь сокращение остатков незавершённого производства за период, что ведёт к экономии на кредитовании или возможности вложения раньше высвободившихся денежных средств в альтернативные мероприятия.
Для внедрения данных изменений необходим человек-лидер, занимающий руководящее положение и имеющий право принимать важные решения и нести за них ответственность. Его следует назначить «агентом изменений», тем, кто будет продвигать идею и контролировать процесс.
Перед внедрением системы требуется провести для всех руководителей подразделений однодневный семинар-тренинг. Менеджеры должны реализовать на своих рабочих местах три первых принципа системы за три месяца.
Каждые три недели они должны участвовать в индивидуально-групповых консультациях по внедрению: сначала обсуждаются накопившиеся вопросы и проблемы в аудитории (в группах по 10-12 человек), а затем все члены группы вместе с консультантами последовательно обходят кабинеты, рабочие места каждого члена группы. При этом решения многих проблем находятся именно в ходе таких обсуждений и посещений. Руководители легко будут перенимать опыт друг друга. Достижение результата должно проверяться по контрольному листку.
Следует изменить организационную схему управления. В первую очередь — изменить штатное расписание. Управление производством доверить мастерам и бригадирам. Все промежуточные управленцы в лице бывших заместителей переводятся в группу развития.
Оценить эффекты от внедрения данного мероприятия до реализации системы 5S сложно, однако, можно на основе опыта российских предприятий предположить, какими будут выгоды при успешной реализации данного проекта (рис. 1) [3].
При успешности внедрения системы 5S возможно перейти к внедрению системы кайдзен (kaizen) [2], которая основана на: ориентации на потребителя, всеобщем контроле качества, кружках качества, системе предложений, автоматизации, дисциплине на рабочем месте, всеобщем уходе за оборудовании, повышении качества, росте производительности и разработке новой продукции. Одна из отличительных особенностей системы в том, что она направлена на разработку предложений и инноваций «снизу вверх», то есть работник делает предложение по улучшению, предложение рассматривается, принимается решение — внедрять его или нет. Далее происходит внедрение предложения, и работник поощряется за его идею (в том числе и в виде процента от экономического эффекта).
Рисунок 1- Ожидаемые выгоды от внедрения бережливого производства
Данные мероприятия повлекут не только несомненный материальный эффект для предприятия, но и изменение корпоративной культуры, выражающиеся в более аккуратном и внимательном отношении к собственному рабочему месту и предприятию в целом, росте рационализаторских предложений. Поощрять такие предложения следует материально (премии от 5 до 15% от заработной платы, организация поездок, экскурсий) и морально в виде грамот, досок почёта и т.д.
Литература
1. Володин, Р.С.Формирование архива документов по системе 5S / Р.С. Володин. -http://www.virtpronet.ru/index.php?do=static&page=5s;
2. Имаи, М. Кайдзен: Ключ к успеху японских компаний/ М. Имаи. – М.: Альпина Бизнес Бук, 2005. – 274 с.
3. Попов, С.Г.Применение методик концепции «Бережливое производство» / С.Г. Попов. — http://ria-stk.ru/mmq/adetail.php?ID=48266.
4. Растимешин, В.Е. Упорядочение / 5S – система наведения порядка, чистоты и укрепления дисциплины с участием всего персонала /В.Е.Растимешин, Т.М.Куприянова. — http://www.tpm-centre.ru/page.php?pageId=106&menuItemTreeCode=050304
5S
Ссылки (изображения) ниже приведут вас ко всем нашим доступным ресурсам 5S, чтобы помочь вам полностью понять этот мощный инструмент бережливого производства; Нажмите на картинку ниже, чтобы получить более подробную информацию о 5S.
Что такое 5S; Определение и преимущества
Узнайте, что такое 5S и какие преимущества может принести вашему бизнесу внедрение этого очень простого, но очень эффективного инструмента бережливого производства.
-
- Что такое 5S
-
- Преимущества 5S
Что такое 5S Lean Преимущества 5S
5 шагов 5S
Подробная информация о 5 шагах 5S, а также о шестом шаге, который добавляют некоторые компании; Безопасность (или 6S).
5S есть; Сейри, Сейтон, Сейсо, Сэйкэцу и Сицукэ. 5S на английском языке: Sort, Straighten, Shine, Standardize и Sustain. Некоторые компании используют 6S, повышающую безопасность, в качестве 6-го шага в методологии.
Внедрение 5S
Руководства по внедрению 5S на рабочем месте или в офисе.
-
- Реализация программы 5S
-
- 5S Офис
Обучение 5S
Помогите обучить ваших сотрудников пониманию и внедрению процесса 5S.
-
- 5S обучение
-
- Курс обучения 5S
-
- Нанять 5S Trainer
5S ресурсов;
ресурсов 5S; от книг и DVD до игр и красных ярлыков. Все, что вам может понадобиться для внедрения 5S.
,Инструменты бережливого производства
Откройте для себя все, что вы когда-либо хотели знать о многих инструментах и методах бережливого производства, а также о том, как их можно эффективно реализовать в своем бизнесе. Мы предлагаем вам полный набор всех идей и инструментов, которые вы найдете в рамках «Бережливое производство» и «Бережливое производство и шесть сигм».
Добро пожаловать в «Инструменты бережливого производства», этот веб-сайт расскажет вам о различных принципах бережливого производства, его многочисленных эффективных инструментах и методах, а также людях, которые способствовали его развитию.Этот сайт также будет держать вас в курсе последних событий в различных отраслях, в которых внедряется бережливое производство.
Прокручивая эту страницу вниз, вы найдете краткие описания различных инструментов и методов бережливого производства и ссылки на страницы, где они описаны более подробно.
Инструменты бережливого производства
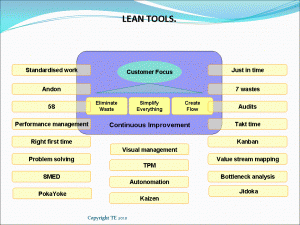
Инструменты бережливого производства
Существует множество различных инструментов бережливого производства, которые вы можете внедрить в своем бизнесе.Вместе они образуют единое целое, которое может быть реализовано как бережливое производство в вашей компании. Эти инструменты наиболее эффективны, если они реализованы вместе, однако многие из них можно использовать по отдельности для решения конкретных проблем в вашем бизнесе.
Если вы хотите получить полную информацию о многих инструментах, которые используются в Lean и Lean Sigma, и о том, для чего они нужны, то взгляните на наш список 50 лучших инструментов Lean .
Бесплатные презентации Lean
Мы также предлагаем вам полный спектр бесплатных загружаемых экономичных презентаций , которые доступны в форматах PowerPoint (pptx) и PDF.Они охватывают многие из различных методов бережливого производства и могут бесплатно использоваться в вашем собственном бизнесе. Мы также предоставляем онлайн-обучение и консультации через нашего тренера по бережливому производству .
Что такое бережливое производство?
Lean в прошлом назывался многими вещами; Производство мирового класса, производство без складских запасов, производство точно в срок и производственная система Toyota (TPS), и это лишь некоторые из них, но что такое бережливое производство?
Lean — это гораздо больше, чем просто способ сократить расходы и избавиться от ненужных отходов.Используя бережливое производство, вы можете быть уверены в том, что улучшаете качество своей работы, а также всегда вовремя доставляете то, что нужно клиенту.
Перейдите по этой ссылке, чтобы ознакомиться с полным описанием бережливого производства и определения бережливого производства.
История бережливого производства
Бережливое производство имеет историю, уходящую на много сотен лет назад, до появления производственных линий Ford модели T и производственной системы Toyota, которую мы знаем сегодня. Знание того, откуда появился Lean и почему он был разработан, может помочь вам лучше понять, что он действительно может для вас сделать.Для полного обсуждения взгляните на историю бережливого производства .
Преимущества бережливого производства
Зачем нам нужно внедрять бережливое производство? Каковы преимущества бережливого производства? Компания Toyota прошла путь от производителя дешевых автомобилей до мирового лидера благодаря внедрению производственной системы Toyota, известной на Западе как бережливое производство.
Внедряя инструменты бережливого производства в свой бизнес, вы получаете возможность сократить отходы, сэкономить деньги и расширить свой бизнес.
Чтобы получить полный обзор анекдотических преимуществ, а также фактическую статистику, взгляните на преимущества бережливого производства .
Принципы и философия бережливого производства
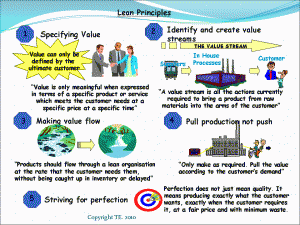
Принципы бережливого производства
Существует пять основных принципов бережливого производства, определенных Womack and Jones в их публикации 1990 года «Машина, которая изменила мир».
Эти принципы:
- Определите ценность, как она воспринимается покупателем.
- Определите поток создания ценности через ваш бизнес.
- Сделайте поток ценностей.
- Извлеките из потока создания ценности.
- Стремитесь к совершенству.
Чтобы узнать больше об этих принципах бережливого производства и о том, как они применяются в вашем бизнесе, перейдите по этой ссылке: Принципы бережливого производства .
Муда, Мури и Мура Пустоши бережливого производства
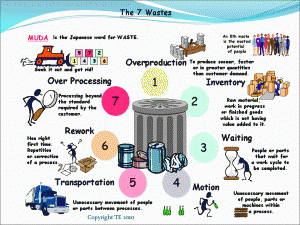
Семь отходов или 7 муд
Отходы — это все, что не добавляет ценности вашему процессу или продукции.Если это не то, за что покупатель был бы рад заплатить, то вам следует постараться удалить это.
Toyota рассматривает три основных направления отходов и идентифицирует их как 3M, или Muda, Mura и Muri :
- Мура: Это пустая трата непоследовательности или неравномерности. Это можно увидеть в пиках и падениях требований нашего времени.
- Мури: это пустая трата вскрыши. Это стресс, который мы создаем для наших сотрудников и процессов из-за чрезмерных требований, отсутствия обучения, плохих инструкций и множества других проблем.
- Muda: это более традиционная идентификация отходов, с которой ассоциируется большинство людей. Обычно это видно на примере Seven Wastes бережливого производства, и это любой процесс, который не добавляет никакой ценности.
Семь отходов постного мяса:
- Транспорт: перемещение товаров из одного места в другое.
- Запасы: от запасов готовой продукции до незавершенного производства (НЗП) и сырья.
- Движение: движение человека или машины в рамках операций.
- Ожидание: время простоя и непродуктивность.
- Перепроизводство: производство того, что сейчас фактически не требуется.
- Over-Processing: выполнение работы, выходящей за рамки того, что фактически требуется.
- Дефекты: все браки и переделки, которые могут быть произведены.
Кроме того, для получения 8 или более отходов постного мяса часто добавляют следующее:
- Талант: это неспособность использовать навыки и знания ваших сотрудников.
- Ресурсы: без надобности расходовать электроэнергию, воду и другие ресурсы.
- Побочные продукты: не использовать ничего, что осталось в ваших процессах.
5S Организация рабочего места
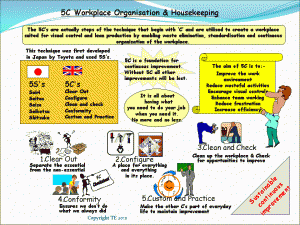
Инструмент 5S для бережливого производства
.
5S — один из основных строительных блоков бережливого производства и один из первых инструментов бережливого производства, с которого вы начнете свою реализацию. Это фундамент Lean, без которого вы не добьетесь успеха.Но , что такое 5S , каковы преимущества у 5S и как мне настроить программу 5S ? 5S предназначен не только для производственных процессов, он также применим в операциях по обслуживанию, а реализация 5S office часто дает больше времени на выполнение заказа, чем те, которые проводятся в вашем цехе. С добавлением Safety в качестве дополнительной буквы «S» мы получаем 6S ; 5S плюс безопасность.
Шаги 5S:
Сортировка или Сейри: Удаление всего беспорядка с территории.
- Выпрямитель или Сайтон: привести в порядок оборудование, инструменты и материалы.
- Sweep или Seiso: чтобы все почистить и проверить.
- Standardize или Seiketsu: внедрить стандартные методы работы.
- Sustain или Shitsuke: привить самодисциплину и сделать процесс частью повседневной практики.
- Многие также добавят шестую букву «S» для безопасности, чтобы сделать его более конкретным этапом процесса.
.
.
Отображение процессов и отображение потока создания ценности
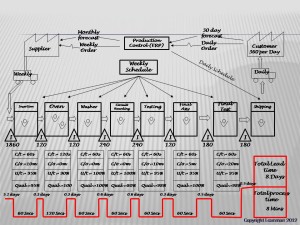
Отображение потока создания ценности (VSM)
Возможность визуализировать, как взаимодействуют и работают ваши процессы, жизненно важна для понимания того, что происходит в вашем бизнесе.
Картирование вашего потока создания ценности с использованием таких идей и методов, как Value Stream Mapping (VSM), простая блок-схема или спагетти-диаграммы — очень эффективный способ выявить и выделить бесполезные шаги в ваших процессах.
Эти карты и диаграммы позволяют быстро определить, где вам нужно улучшить свои процессы. Вы также можете создавать карты будущего состояния и планы действий, чтобы упростить вашу работу и добиться улучшений во всем, что вы делаете.
.
.
Производство точно в срок и Канбан
Производство «точно в срок» или JIT — один из основных столпов бережливого производства. Все дело в том, чтобы делать то, что клиент хочет, когда он этого хочет, где он этого хочет, и в запрошенных количествах без каких-либо задержек на складе.
Это требует сокращения запасов и перехода к работе с небольшими партиями. Это также требует, чтобы вы улучшили и сбалансировали поток ваших процессов.Идеальный процесс — это тот, в котором у вас есть единый поток; вы создадите только один продукт, когда это потребуется.
Как правило, вам потребуется использовать методику замены штампа за одну минуту (SMED), чтобы сократить время настройки и уменьшить размер партии.
Производство «точно вовремя» — это еще и «тяговое производство». Вместо того, чтобы планировать и продвигать производство через свои процессы, вы извлекаете продукты из процессов по мере их заказа. Мы внедряем Kanban , чтобы обеспечить четкий поток без чрезмерного планирования или инвентаризации.
Канбан — это простой метод сигнализации предшествующим процессам, что делать и когда. Это позволяет нам втягивать материалы по мере необходимости, не создавая чрезмерных запасов.
.
Кайдзен
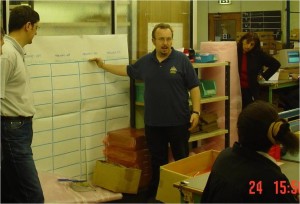
Событие кайдзен
.
Kaizen — это постоянное улучшение каждого процесса вашего бизнеса. Это можно сделать путем постоянного улучшения или с помощью специального модуля Kaizen Blitz , предназначенного для быстрого улучшения конкретной области вашего бизнеса.
Традиционный кайдзен — это командная инициатива, направленная на использование всего персонала в данной области для постоянного улучшения всего, что они делают. Это постоянный процесс, цель которого — делать небольшие постепенные улучшения неделя за неделей.
Блиц кайдзен обычно проводится экспертами и направлен на постепенное улучшение процесса. Обычно у проекта есть конкретная цель, например, повышение эффективности или уменьшение дефектов. Эти проекты обычно длятся около недели и могут значительно улучшить процесс.
Дзидока
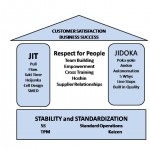
Дзидока — один из столпов дома Лин
.
Одна из опор производственной системы Toyota и, следовательно, бережливого производства; Дзидока — это построенное на качестве.
Включает в себя такие идеи, как:
,5S — Каковы пять «S» бережливого производства?
Глоссарий качества Определение: пять S (5S)
5S определяется как методология, результатом которой является чистое, незагроможденное, безопасное и хорошо организованное рабочее место, помогающее сократить отходы и оптимизировать производительность. Он разработан, чтобы помочь создать качественную рабочую среду как физически, так и морально. Философия 5S применима в любой рабочей области, подходящей для визуального контроля и бережливого производства. Состояние 5S на рабочем месте имеет решающее значение для сотрудников и является основой первых впечатлений клиентов.
Инструмент качества 5S образован от пяти японских терминов, начинающихся с буквы «S», используемых для создания рабочего места, подходящего для визуального контроля и бережливого производства. Основы 5S просты для изучения и их важно реализовать:
- Seiri: Для отделения необходимых инструментов, деталей и инструкций от ненужных материалов и удаления ненужных.
- Seiton: Для аккуратного размещения и идентификации деталей и инструментов для простоты использования.
- Seiso: Провести зачистку.
- Seiketsu: Ежедневно проводить seiri , seiton и seiso для поддержания рабочего места в идеальном состоянии.
- Сицукэ: Чтобы сформировать привычку всегда следовать первым четырем S.
Ниже японские термины переведены на англоязычную версию 5S.
Японский | Переведено | Английский | Определение |
Сейри | организовать | сорт | Удалите все ненужное, отделив необходимые инструменты, детали и инструкции от ненужных материалов. |
Сейтон | упорядоченность | комплект под заказ | Организуйте все, что осталось, аккуратно расположив и обозначив детали и инструменты для простоты использования. |
Seiso | чистота | блеск | Очистите рабочую зону, проведя кампанию по уборке. |
Seiketsu | стандартизировать | стандартизировать | Запланируйте регулярную очистку и техническое обслуживание, ежедневно проводя seiri , seiton и seiso . |
Сицукэ | дисциплина | сустейн | Сделайте 5S своим образом жизни, сформировав привычку всегда следовать первым четырем S. |
Выгоды от внедрения программы бережливого производства 5S включают:
- Повышенная безопасность
- Повышенная доступность оборудования
- Меньше брака
- Сниженные затраты
- Повышенная маневренность и гибкость производства
- Повышение морального духа сотрудников
- Лучшее использование активов
- Повышение имиджа предприятия для клиентов, поставщиков, сотрудников и руководства
Five S (5S) Пример: контрольный список диагностики сканирования на рабочем месте
5S, пример
Во время встреч с внутренними и внешними заинтересованными сторонами группа проекта по регистрации в программе Medicaid Kaiser Permanente Colorado использовала инструмент Lean 5S для улучшения шаблона регистрации, а также процесса шаблонов.Они реализовали столпы 5S следующим образом:
- Поля были отсортированы и ненужные поля удалены.
- Поля были установлены в порядок на основе ввода заинтересованных сторон.
- Команда осветила , создав базу данных Microsoft Access, которая не допускала бы повторяющихся записей.
- Электронная таблица была стандартизирована , защищая ее и делая из нее шаблон.
- Самоподдерживающаяся система была создана с использованием Microsoft Access (для контроля формата данных и дублирования) и шаблонов Microsoft Excel (для контроля формата и порядка электронных таблиц).
Прочтите полный пример исследования: Оптимизированная система набора дает большие результаты для руководителя здравоохранения (PDF)
Вы также можете искать статьи, тематические исследования и публикации по ресурсам 5S.
Книги
5S для сервисных организаций и офисов
Бережливые больницы
Статьи
Все — 5S: простой, но эффективный подход к рациональному использованию, применяемый в центре предварительного тестирования ( Журнал управления качеством, ) Центр предварительного тестирования применил 5S к процессу потока пациентов, оптимизируя этапы и устраняя ненужные затраты.Результаты показывают, что структура 5S является эффективной и простой моделью для разработки и улучшения процессов.
Эффективность офиса ( Quality Progress ) Метод бережливого производства 5S часто используется в производстве, но его можно адаптировать к офисным условиям, чтобы повысить эффективность информационных рабочих процессов. В частности, лучшая организация и управление информационными потоками позволяет работникам умственного труда принимать более обоснованные решения о расстановке приоритетов и выполнении задач.
Видео
Использование 5S в повседневной жизни Член ASQ Александр Такер, химик из Capsugel, использовал инструмент 5S в своей домашней жизни.Вы не перестанете улыбаться, когда он с юмором рассказывает о том, как он организовал свою ванную комнату, запланировал поездки в продуктовый магазин и даже научил свою собаку быть качественной собакой.
Адаптировано из Quality Essentials: Справочное руководство от А до Я , ASQ Quality Press.
,Реализация программы 5S
Программа 5S
Любой инструмент бережливого производства, стратегия улучшения бизнеса и даже 5S потерпят неудачу, если у вас нет видения и стратегии в отношении того, куда вы ведете свой бизнес. 5S должны стать частью общей цели вашего бизнеса; это не самоцель.
Отсутствие четкого видения и стратегии для будущего вашего бизнеса не позволит вам четко определить, чего вы пытаетесь достичь с помощью программы 5S.5S должны стать частью пути к этому видению, и каждый в вашей организации должен знать, каково это видение.
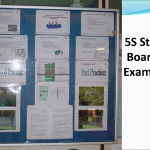
Раскадровка внедрения 5S
Toyota, несомненно, является ведущим производителем автомобилей в мире, у них есть четкое видение своего будущего и они знают, чего они пытаются достичь. Это видение доводится до сведения всех сотрудников организации, и каждый знает, каков их вклад в достижение этих целей.
Если ваши сотрудники не видят, какой вклад они вносят в будущее компании и каково это будущее, им будет трудно взять на себя обязательства перед вами и знать, в каком направлении двигаться.Инициатива 5S без четких целей не будет столь же эффективной, как инициатива, в которой каждый знает общие цели компании по ее реализации.
Управленческий взнос и обучение по программе 5S
Как только у вас появится четкое представление о том, в каком направлении вы движетесь со своей компанией, вы можете заручиться поддержкой своей управленческой команды. Им потребуется обучить принципам бережливого производства, уметь определять семь отходов бережливого производства и другие отходы (муда, мури и мура), а затем пройти обучение применению 5S.
Ваше руководство должно понимать и применять идеи 5S самостоятельно, чтобы служить примером для других ваших сотрудников. Было бы сложно мотивировать ваших сотрудников поддерживать порядок на рабочем месте, если каждый раз, проходя мимо стола своего менеджера, они видели груды неухоженного загромождали.
Команда программы 5S / отбор пилотов
Было бы неразумно пытаться внедрить 5S во всей организации за один раз (если только у вас нет небольшой компании), лучше выбрать одну область, в которой сосредоточить свои усилия, и предоставить демонстрационный образец для остальной части организации.
На мой взгляд, было бы лучше выбрать худшую область в компании, чтобы показать, чего можно достичь и какие изменения это может сделать. Если ваша компания больше, выберите несколько областей, но включите области, отличные от цеха, 5S и бережливое производство в целом применимы к вашему офису (офис Lean 5S) и зонам обслуживания, как и к производству.
Убедитесь, что куратор области, в которой будет запущена реализация вашей программы 5S, заинтригован, именно он будет руководить вашей командой в данной области.Важно, чтобы территория владела своими улучшениями и несла ответственность за их постоянное улучшение. Также выберите людей из-за пределов области, чтобы присоединиться к команде, люди из областей, которые будут следовать пилотной области, являются хорошей идеей, поскольку тогда у них будет некоторый опыт, когда дело доходит до внедрения 5S в своих областях. Посторонние также полезны, поскольку они задают много вопросов и задают вопросы, действительно ли что-то требуется и как это делается.
Руководство области должно иметь возможность продемонстрировать поддержку и позволить команде внести изменения, которые, по их мнению, они должны внести, в целом изменения, инициированные 5S, являются либо нулевыми, либо очень низкими, поэтому следует выделить небольшой бюджет для команды.Более крупные расходы должны проходить через маршруты утверждения, как и любые другие расходы.
Обучение группы внедрения 5S
Вся команда должна быть обучена видению и целям компании и иметь четкое представление о том, чего компания пытается достичь с помощью них и их реализации программы 5S. Им необходимо иметь четкое представление о семи отходах бережливого производства и обзор основных принципов бережливого производства. Обладая этими знаниями, они будут готовы приступить к внедрению 5S.
Если у вас нет штатного специалиста, который бы облегчил вашу программу 5S, вам нужно будет нанять консультанта по 5S или инструктора по бережливому производству / 5S, который сделает эту работу за вас. Классное обучение неэффективно для внедрения 5S, за исключением базового обзора и метода. 5S лучше всего усваивается через практические действия и внутренние учебные курсы по 5S, поэтому роль консультанта / инструктора должна заключаться в том, чтобы помогать и мотивировать команду, а также удерживать ее в правильном направлении.
5S Программа видео
Внедрение 5S
Прежде всего, возьмите цифровую камеру и сделайте много снимков местности, в которой вы будете проводить 5S.
Изучите показатели процесса и убедитесь, что они надежны и отражают улучшения, которые вы хотите внести. Если нет, создайте новые показатели производительности и соберите данные, чтобы создать основу для измерения улучшений производительности. Предложения включают такие вещи, как производительность в человеко-час, количество дефектов и переделок, производительность доставки и т. Д.
По моему опыту, лучший метод реализации — это провести первые три этапа 5S как один блиц, имея всю команду в этой области для устранения весь беспорядок и все убрать, а затем аккуратно расставить вещи в качестве отправной точки.
Это займет от двух до трех дней в зависимости от размера и сложности области, в которой вы внедряете 5S. В конце этого с помощью вашего фасилитатора группа должна удалить весь беспорядок, очистить территорию и организовать все компоненты, инструменты, оборудование и т. Д.
На этом этапе у них, вероятно, будет список изменений или необходимого оборудования, которое потребуется неделю или две, чтобы завершить и дать дальнейшие успехи в отношении организации и размещения вещей в этой области.Поэтому на этом этапе часто стоит сделать перерыв на неделю или две, прежде чем перейти к четвертой стадии 5S. В это время команда должна встречаться каждый день, чтобы анализировать, как все работает, и какие дополнительные улучшения они могут внести.
Фасилитатор (консультант / инструктор) должен вернуться примерно через 2 недели, и команда должна начать работу над 4-м этапом 5S и приступить к стандартизации своих операций. Создавайте графики и инструкции по очистке, создавайте стандартные инструкции по эксплуатации (очень легко с сегодняшними компьютерными пакетами и цифровой камерой) и т. Д.Этим этапом часто пренебрегают во многих реализациях 5S.
В дополнение к этому группа должна создать стандартные аудиты для оценки и выставления баллов в своей области, чтобы их можно было контролировать на постоянной основе.
Следует сфотографировать улучшенную рабочую зону и установить раскадровку 5S, чтобы показать полученные улучшения. Я также предлагаю, чтобы команде было разрешено выступить с презентацией перед руководством и остальной частью организации, чтобы продемонстрировать свои достижения.
Обзор программы 5S
После того, как команда выполнила все вышеперечисленное, они должны обойти и сделать больше фотографий, поместив примеры до и после на доску историй 5S, которая будет размещена в области, показывая всем, какие улучшения были сделаны.
Следует также проводить сравнения с базовыми показателями, которые были начаты до 5S, после чего можно оценить степень улучшения. Должно произойти заметное повышение эффективности и качества работы.
Команда должна воспользоваться этой возможностью, чтобы сделать краткую презентацию руководству и остальной части компании относительно того, как прошел процесс и какие улучшения они внесли.
Развертывание программы 5S
Выберите следующую область (области), в которой вы будете внедрять 5S как часть своей программы 5S, и повторите указанные выше шаги для каждой области, включите опытных людей из вашей начальной области в следующую команду, чтобы убедиться, что обучение на основе первого внедрения 5S программы выполняются.
По мере того, как вы расширяетесь в своей организации, вы, возможно, захотите обдумать идею ежемесячного или ежеквартального присуждения награды 5S для лучших областей, дайте своим сотрудникам то, к чему стремиться.
5S и PDF
Реализация программы 5S — Бесплатная загрузка презентации 5S PowerPoint
Внедрение программы 5S — загрузка 5S PDF.
Шаги 5S для вашей программы внедрения 5S
5S Seiri (сортировка, очистка, классификация) — это этап, на котором вы отделяете беспорядок от инструментов, оборудования, материалов и машин, которые вам действительно нужны.
5S Seiton (Выпрямить, Упростить, Установить по порядку, Настроить) — это шаг, на котором вы начинаете размещать свои элементы эффективным и эргономичным способом для повышения эффективности, качества и безопасности.
5S Seiso (Sweep, shine, Scrub, Clean and Check) — это этап, на котором вы очищаете всю область (и держите ее в таком состоянии), чтобы вы могли видеть, когда что-то идет не так, например, утечка масла.
5S Seiketsu (стандартизация, стабилизация, соответствие) — это этап, на котором вы разрабатываете стандартные способы работы в своих рабочих ячейках с помощью визуального управления и стандартных рабочих инструкций.
5S Shitsuke (устойчивость, самодисциплина, обычаи и практика) — это то место, где вы гарантируете, что 5S станет частью культуры вашей организации.
Ресурсы 5S для реализации вашей программы 5S
Эти ресурсы помогут вам при внедрении 5S;
- 5S Карманные руководства, книги и карточки в качестве портативного справочника. DVD-диски и видео
- 5S могут помочь вам показать вашим сотрудникам, как следует реализовать хорошую программу 5S.
- Книги по 5S и электронные книги по 5S могут дать вам подробные пошаговые инструкции по внедрению 5S.
- 5S Расходные материалы, когда вы внедряете 5S, например стеллажные и теневые доски.
- 5S обучающие игры и симуляторы для демонстрации реализации 5S.
- 5S Плакаты для напоминания сотрудникам об этапах программы 5S.
Если у вас есть какие-либо вопросы или замечания относительно реализации программы 5S или вы хотите поделиться успехом своей собственной реализации 5S, используйте область ниже.
,
Добавить комментарий
Комментарий добавить легко