пять шагов к идеальному рабочему месту
5S – сокращение от “5 Steps” (пять шагов) представляет собой инструмент для обеспечения системы бережливого производства, рационализации рабочего места. Это не “стандартизация уборки”, а философия экономного, успешного, бережливого производства. Система была разработана в послевоенной Японии, в компании Toyota.
Цели 5S• создание комфортного психологического климата, стимулирование желания работать; Что такое 5S5S – это пять японских слов, описывающих цикл, состоящий из последовательных шагов: Шаг 1. Сортировка (cэири) — чёткое разделение вещей на нужные и ненужные и избавление от последних. Шаг 2. Соблюдение порядка (сэитон) — аккуратность, организация хранения необходимых вещей, которая позволяет быстро и просто их найти и использовать. Шаг 3. Содержание в чистоте (сэисо) — уборка, соблюдение рабочего места в чистоте и опрятности. Шаг 4. Стандартизация (сэикэцу) — поддержание порядка, необходимое условие для выполнения первых трёх правил. Шаг 5. Совершенствование (сицукэ) — формирование привычки, воспитание привычки точного выполнения установленных правил, процедур и технологических операций. | ![]() |
1. Сортировка2. Соблюдение порядка3. Содержание в чистоте4. Стандартизация5. Совершенствование
Шаг 1. Сортировка
Сортировка – означает, что вы высвобождаете рабочее место от всего, что не понадобиться при выполнении текущих производственных операций.
Рабочие и руководители часто не имеют привычки избавляться от предметов, которые больше не нужны для работы, сохраняя их поблизости «на всякий пожарный случай». Обычно это приводит к недопустимому беспорядку или к созданию препятствий для перемещения в рабочей зоне. Удаление ненужных предметов и наведение порядка на рабочем месте улучшает культуру и безопасность труда. Чтобы более наглядно продемонстрировать, сколько лишнего скопилось на рабочем месте, можно на каждый предмет-кандидат на удаление из рабочей зоны повесить красный ярлык (флажок).
Все сотрудники вовлекаются в сортировку и выявление предметов, которые:
• должны быть перемещены в более подходящее место для хранения;
• должны быть оставлены и для них должны быть созданы и обозначены свои места.
Необходимо чётко обозначить «зону красных ярлыков» предметов с красными флажками и тщательно её контролировать. Предметы, остающиеся нетронутыми свыше 30 дней, подлежат переработке, продаже или удалению.
Шаг 2. Соблюдение порядка
Соблюдение порядка – означает определить и обозначить «дом» для каждого предмета, необходимого в рабочей зоне, сделать расположение рациональным. Иначе, если, например, производство организовано по сменам, рабочие разных смен будут класть инструменты, документацию и комплектующие в разные места. В целях рационализации процессов и сокращения производственного цикла крайне важно всегда оставлять нужные предметы в одних и тех же отведённых для них местах. Это ключевое условие минимизации затрат времени на непродуктивные поиски.
Шаг 3. Содержание в чистоте
Содержание в чистоте – значит обеспечить оборудованию и рабочему месту опрятность, проводить современную уборку, достаточную для проведения контроля, и постоянно поддерживать её. Уборка в начале и/или в конце каждой смены обеспечивает немедленное определение потенциальных проблем, которые могут приостановить работу или даже привести к остановке всего участка, цеха или завода.
Шаг 4. Стандартизация
Шаг 5. Совершенствование
Совершенствование – означает то, чтобы выполнение установленных процедур превратилось в привычку.
Мероприятия, лежащие в основе 5S (сортировка, рациональное расположение, уборка, стандартизация и совершенствование), абсолютно логичны. Они представляют собой базовые правила управления любым продуктивно работающим отделом. Однако именно системный подход, который система 5S применяет к этим мероприятиям, и делает ее уникальной.
Кодовое значение цвета в системе 5S
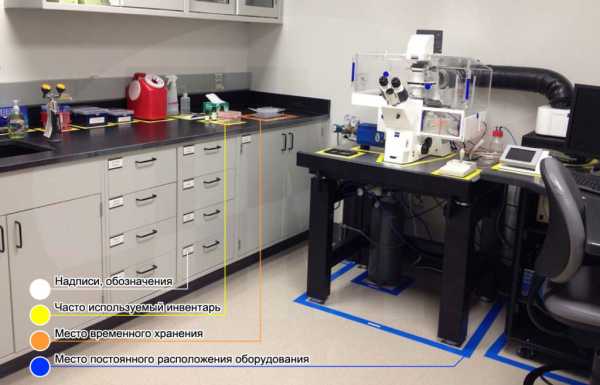
Пример использования напольных лент 3М
Примеры (фото) ДО и ПОСЛЕ внедрения 5S
Для реализации 5S Вам пригодятся
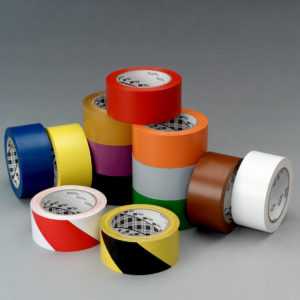
Цветные ленты
Износостойкие, эластичные самоклеющиеся цветные ленты из ПВХ. Также доступны в виде стрелок, следов, кругов.
Знаки безопасности
Различные знаки безопасности, указатели, таблички в соответствии с нормативами.
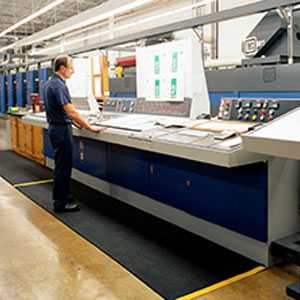
Напольные покрытия
Противоусталостные и противоскользящие напольные покрытия сделают помещение безопаснее, удобнее и уютней.
tmark.ru
описание, особенности, принципы и отзывы
Руководитель любого предприятия, независимо от сферы деятельности, мечтает, чтобы прибыль росла, а производственные затраты оставались неизменными. Добиться такого результата помогает система «5С» на производстве (в английском варианте 5S), основывающаяся только на рациональном использовании внутренних резервов.
Создавалась эта система не с чистого листа. Нечто подобное еще в конце XIX века предлагал американец Фредерик Тейлор. У нас в России этим занимался ученый, революционер, философ и идеолог А.А. Богданов, издавший в 1911 году книгу о принципах научного менеджмента. На основе изложенных в ней положений в СССР внедряли НОТ, то есть научную организацию труда. Но наиболее совершенной стала предложенная японским инженером Тайити Оно и внедренная им на заводе Toyota Motor система «5С» на производстве. Что это такое, и почему японская система стала такой популярной?
Дело в том, что в ее основе лежит простой принцип, не требующий затрат. Он заключается в следующем — каждый работник, от уборщицы до директора, должен максимально оптимизировать свою часть в общем рабочем процессе. Это приводит к увеличению прибыли производства в целом и к росту доходов всех его сотрудников. Сейчас эстафету внедрения системы «5С» подхватили предприятия во всем мире, включая Россию. В этой статье мы попытаемся убедить скептиков в том, что японское ноу-хау действительно работает, причем абсолютно в любой сфере деятельности.
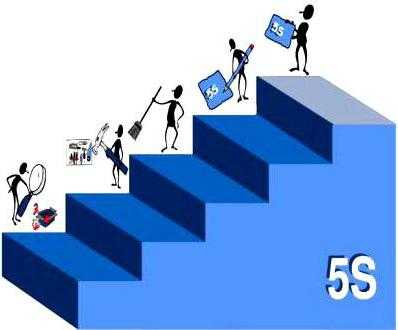
Система «5С» на производстве, что это такое
Международное 5S расшифровывается, как пять шагов («шаг» по-английски step). Некоторые экономисты и пропагандисты нового отношения к труду объясняют название пятью японскими постулатами, последовательно внедряемыми в системе 5S: сэири, сэитон, сэисо, сэикэцу и сицукэ. Для нас ближе и понятнее наши родные «5С» — пять последовательных шагов, которые нужно выполнить, чтобы добиться процветания своего производства. Это:
1. Сортировка.
2. Соблюдение порядка.
3. Содержание в чистоте.
4. Стандартизация.
5. Совершенствование.
Как видим, ничего сверхъестественного система «5С» на производстве не требует. Возможно, именно поэтому к ней пока можно встретить недоверие и несерьезное отношение.
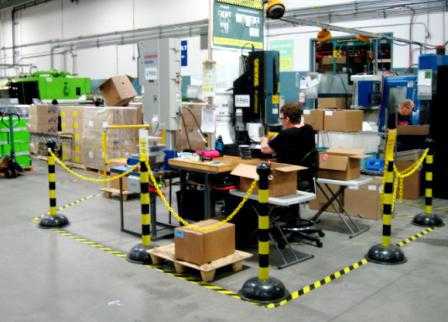
Этапы создания системы
Мудрый японец Тайити Оно, который, благодаря внедрению на заводе по производству «Тойот» своих методик, сумел дослужиться от инженера до генерального директора, обратил внимание, как много потерь происходит из-за различных неувязок и накладок. Например, на конвейер не поставили вовремя какие-нибудь мелкие винтики, и в результате встало все производство. Или наоборот, деталей подали с запасом, они оказались лишними, и в результате кому-то из сотрудников пришлось везти их обратно на склад, а значит, тратить на пустую работу свое время. Тайити Оно разработал концепцию, которую назвал «точно в срок». То есть на конвейер теперь поставлялось ровно столько деталей, сколько нужно.
Можно привести и другие примеры. Система «5С» на производстве также включала в себя концепцию «канбан», что по-японски значит «рекламная вывеска». Тайити Оно предложил на каждую деталь или каждый инструмент цеплять так называемую бирку «канбан», в которой давалась вся необходимая информация по детали или инструменту. В принципе, она применима к чему угодно. Например, к товарам, медикаментам, папкам в офисе. Третьей концепцией, на которой основывается система «5С» на производстве, стало понятие «кайдзен», означающее непрерывное совершенствование. Придумывались и другие концепции, которые подошли лишь для узкоспециализированных производственных процессов. В этой статье мы их рассматривать не будем. В итоге всех опробованных на практике нововведений и сформировалось 5 шагов, применимых к любому производству. Разберем их подробно.
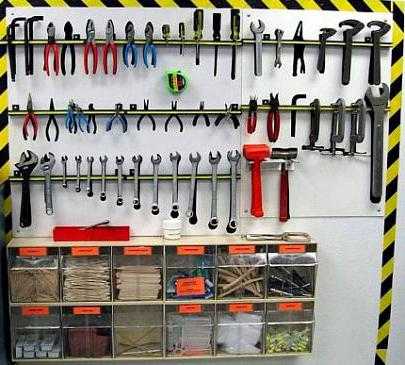
Сортировка
У многих из нас на рабочих столах скапливаются предметы, которые, в принципе, не нужны. Например, старые формуляры, не используемые файлы, черновики расчетов, салфетка, на которой стояла чашка кофе. А среди этого хаоса могут находиться нужные файлы или документы. Основные принципы системы «5С» подразумевают оптимизировать свой рабочий процесс, то есть сделать так, чтобы не тратилось время на поиск нужных вещей среди завалов ненужного. Это и есть сортировка. То есть на рабочем месте (возле станка, на столе, в мастерской – где угодно) все предметы раскладываются на две стопки – нужное и ненужное, от которого необходимо избавиться. Далее все нужное раскладывается на следующие стопки: «используется часто и постоянно», «используется редко», «почти не используется». На этом сортировка закончена.
Соблюдение порядка
Если просто разобрать предметы, толку не будет. Нужно эти предметы (инструменты, документы) разложить в таком порядке, чтобы используемое постоянно и часто очутилось на виду или так, чтобы его можно было быстро взять и легко положить назад. То, что используется редко, можно отправить куда-нибудь в ящик, но к нему нужно прикрепить бирку «канбан», с тем, чтобы через время можно было легко и безошибочно его найти. Как видим, система «5С» на рабочем месте начинается с самых простых шагов, но на деле она оказывается очень эффективной. А кроме того, она повышает настроение и желание трудиться.
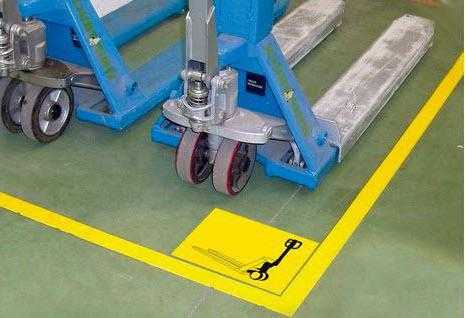
Содержание в чистоте
Этот третий шаг является для многих самым логичным. Соблюдать чистоту нас учат с детства. На производстве она тоже необходима, причем, чистыми должны быть не только столы офисных работников или шкафы в учреждениях общепита, но и станки, подсобные помещения уборщиц. В Японии сотрудники бережно относятся к своим рабочим местам, трижды в день их убирают – с утра перед работой, в обеденный перерыв и вечером, по окончании трудового дня. Кроме того, у них на предприятиях введена специальная маркировка участков, позволяющих соблюдать на производстве порядок, то есть разными цветами отмечены участки готовой продукции, складирования определенных деталей и так далее.
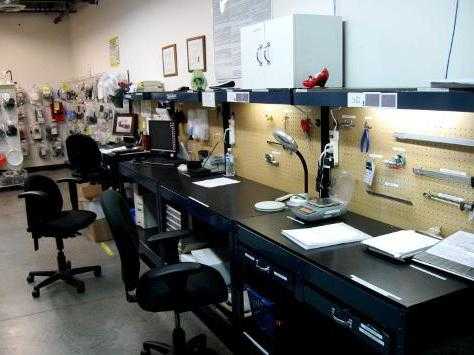
Стандартизация
Принципы стандартизации придумал еще Тайити Оно. Широко использует их и современная система 5S. Управление производством, благодаря стандартизации, получает замечательный инструмент контроля за всеми процессами. В результате быстро устраняются причины отставания от графика и исправляются ошибки, приводящие к выпуску некачественной продукции. На заводе Toyota Motor стандартизация выглядела так: мастера составляли ежедневные планы работ, на рабочих местах вывешивались точные инструкции, в конце трудового будня специальные работники проверяли, какие за день произошли отступления от плана и почему. Это и есть основное правило стандартизации, то есть точные инструкции, планы работ и контроль за их выполнением. Сейчас на многих предприятиях, например, на заводах ENSTO в Эстонии, вводится премиальная система работников, четко выполняющих положения системы «5С» и на основе этого повышающих свою производительность, что является отличным стимулом принять эту систему, как образ жизни.
Совершенствование
Пятый шаг, на котором завершается система «5С» на производстве, основан на концепции кайдзен. Она означает, что все работники, независимо от занимаемой должности, должны стремиться усовершенствовать процесс работы на вверенном им участке. Философская суть кайдзен заключается в том, что вся наша жизнь каждый день становится лучше, а коль работа – это часть жизни, она тоже не должна оставаться в стороне от улучшений.
Поле деятельности тут широкое, ведь пределов у совершенства не существует. Согласно понятиям японцев, работники сами должны хотеть улучшить свой производственный процесс, без указаний и принуждений. Сейчас во многих организациях создаются команды рабочих, следящих за качеством продукции, обучающих своему положительному опыту других, помогающих добиваться совершенства.
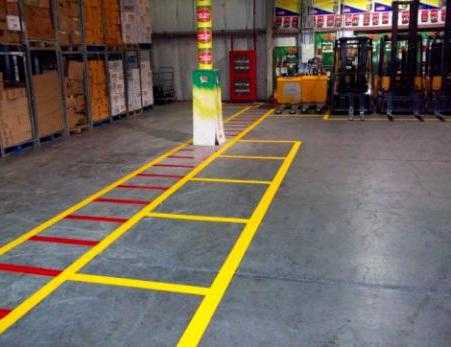
Основные ошибки
Чтобы система «5С» начала работать, мало ее организовать или взять на работу сотрудников, которые будут заставлять своих коллег ее внедрять. Тут важно, чтобы люди осознали полезность этого новшества и приняли его как стиль жизни. Внедрение системы «5С» в России на производстве сталкивается с трудностями именно по причине того, что наш русский менталитет отличается от японского. Для многих наших производств характерно следующее:
1. Работники, особенно если для них нет поощрительных стимулов, не стремятся увеличить прибыль предприятия. Они спрашивают, зачем стараться сделать начальника еще богаче, если у него и так все есть.
2. Сами руководители не заинтересованы во внедрении системы «5С», потому что не видят в ней целесообразности.
3. Многие директивы, «спускаемые сверху», привыкли выполнять только для «галочки». В Японии наблюдается совсем другое отношение к своему труду. Например, тот же Тайити Оно, внедряя систему «5С», думал не о личной выгоде, а о выгоде компании, в которой он был всего лишь инженером.
4. На многих предприятиях внедряется насильно система «5С». Бережливое производство, подразумевающее устранение потерь всех видов (рабочего времени, сырья, хороших работников, мотивации и прочих показателей) при этом не получается, так как работники начинают на подсознательном уровне противиться нововведениям, что в итоге сводит все старания к нулю.
5. Руководители, внедряющие систему, не полностью понимают ее суть, из-за чего возникают сбои в налаженных процессах производства.
6. Стандартизация часто перерастает в бюрократию, хорошее дело обрастает указаниями и директивами, которые только мешают работе.
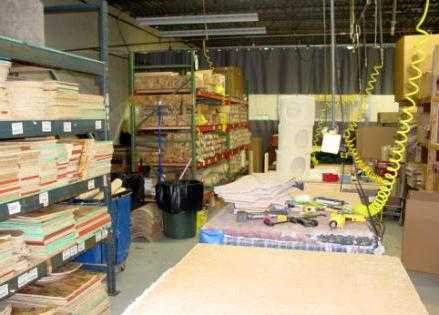
Отзывы
Россияне, у кого введена система «5С» на производстве, отзывы об этом новшестве оставляют весьма неоднозначные. Отмечаемые плюсы:
- приятнее находиться на рабочем месте;
- не отвлекают от работы ненужные мелочи;
- более четко идет рабочий процесс;
- снизилась усталость в конце смены;
- немного возросла зарплата за счет увеличения производительности труда;
- снизился производственный травматизм.
Отмечаемые минусы:
- проводя сортировку, заставляют выбрасывать все подряд;
- стандартизация привела к увеличению бюрократии;
- введение системы «5С» не на всех участках предприятия усугубило проблемы;
- постановка на первое место системы «5С» отодвинула на второй план такие важные вопросы, как нехватка запчастей.
fb.ru
Система 5с на производстве что это такое
Есть ли какой не затратный способ увеличить производительность труда? Спросили предприниматели и бизнесмены. Есть – это система 5S. Расскажу про систему 5С на производстве, что это такое, с примерами и практическими рекомендациями.
Содержание
Система 5С на производстве что это такое
Примеры из жизни производства «До»
Как внедрить 5S – 1 этап
Внедряем практически 5S – 2 этап
Как 5S внедрить на практике – 3-5 этап
Примеры из жизни производства «После»
Как не надо внедрять 5S
Система 5С на производстве что это такое
Одно время, работая в крупной российской организации, мы внедряли систему 5С. Позже я стала обучать сотрудников и проводить тренинги по внедрению 5S (допускается название и»С» и «S») . Это было начальное звено огромных трансформаций, которые пошли на пользу бизнесу.
Эта система позволила сотрудникам экономить время и силы на выполнение более продуктивных задач, на выполнение бизнес-плана.
Поэтому, зная тему изнутри, объясню простыми словами, что такое 5С. Прежде всего, это разумная организация своего труда. Цель – сэкономить время и силы, борьба с потерями, неэффективными движениями.
Это не только сокращение времени на операцию, повышение производительности и изготовление большего количества деталей в одну единицу времени, но и безопасность.
Расшифровка 5S:
- Sorting — Сортируй. Сортировка нужных и лишних вещей. Нужные – оставляй, ненужное – выброси! УБОРКА
- Set in Order — Соблюдай порядок. У каждого предмета свое место: где взял, туда и положи обратно. ПОРЯДОК
- Sweeping – Содержи в чистоте. Вытри пыль и дыши свободно. ЧИСТОТА.
- Standardizing – Стандартизируй. После многих попыток выбери самое удобное расположение вещей, и пусть так будет всегда и на каждом аналогичном участке. СТАНДАРТ
- Sustaining the discipline – Совершенствуй. Пусть применение принципов 5 с войдет в привычку и станет незаменимым спутником на рабочем месте, а не хаос – обузой. Периодично смотри критично на свое рабочее место «Что можно улучшить?» УЛУЧШЕНИЯ
Для получения полно представления о системе 5S приведу примеры ситуации «До» внедрения на производстве.
Примеры из жизни производства «До»
Цех со станками ЧПУ. В цеху работают 3 смены, 6 бригад – операторы станков с ПУ (пультом управления). Ежедневно вытачивают детали для машиностроения, используют в своей работе инструменты для измерения. Пересменок не на рабочем месте, встречаются в раздевалке.
Ситуация «До» внедрения
Пример 1
Начало смены начиналось с поиска нужного инструмента, иногда, утро начиналось совсем не с песни :).
Инструменты хранились в ящике того рабочего, кто последний использовал. Попользовался штангенциркулем и бросил в ящик, закрыл на ключ. А завтра ушел на больничный. Станки полдня простаивают, потому что никто не знает, где инструмент.
Пример 2
На том же производстве, но уже на рабочем месте в бухгалтерии. Вышестоящая организация запросила срочно сверку по деталям, отгруженным полгода назад. Мария Ивановна, ответственная за этот участок, проходила медкомиссию в этот день.
Отчет нужен срочно, с выборкой данных по браку и калибровке. Коллеги попытались помочь, потратили много времени, но найти в компьютере нужный документ не смогли. С бумажным вариантом дела обстояли еще сложнее, отчет нужно было «поискать» в стопке в шкафу.
Пример 3
На склад, на этом же производстве, обратился оператор станка за прибором, нутромер вышел из строя. Кладовщик искал нужный инструмент 40 минут, потому что сменщик «куда-то задевал».
Если посчитать все временные потери в примерах, и перевести в цифры – минуты – в часы – а потом в зарплату. За год получится внушительная сумма.
Даже если каждый работник простаивает (ожидает, ищет, ходит) по 20 минут в день, 247 рабочих дней 4940 минут – 82 часа в год по !одному! сотруднику. Сколько человек работает на производстве?!
В примерах описаны ситуации в разных подразделениях не случайно. Система 5С должна охватывать всю структуру. Везде, во всех отделах, цехах, начиная от руководителя и секретаря, соблюдайте единые стандарты работы.
Как внедрить 5S – 1 этап
1 этап – уборка, сортировка и удаление ненужного
- Определение критериев для сортировки.
Отложите все необходимое в сторону. Все, что подвергается сомнению в другое место. Что не используется – либо выбросить, либо в места дальнего хранения. Знаете, в каждом доме есть антресоли, куда складывается вещи, которые редко используются.
В месте дальнего хранения нужно раз в полгода проводить ревизию. Если не использовалось в течение этого периода, выкидывать. И 3 «кучка» — это вещи, подвергающиеся сомнению: нужно-не нужно.
На начальном этапе мы устраивали «субботники» после каждого рабочего дня целую неделю. Потом шутили: «копили добро годами, а разобрать хотим за час»
- Определение места временного хранения – «зона хаоса»
Сделать временную зону хаоса, куда помещать все предметы «без решения». Обращаю внимание, временную. Через месяц этого понятия быть не должно. Пометьте красным маркером или изолентой «место хаоса».
Система 5 гибкая система, ее необходимо подстраивать под компанию и коллектив. Где-то можно сделать общую временную зону, у кого-то это будет индивидуальное, свое место «неразберихи».
Удалить ненужные предметы – значит сократить количество предметов до нужного в данное время. Сортировка, произведенная правильно, перестает быть лишь наведением порядка, фактически она становится инструментом для полного обновления рабочего места.
Внедряем практически 5S – 2 этап
2 этап. Навести порядок
На данном этапе рисуется карта помещения, где внедряется 5S. Делаются замеры передвижения, перемещений «До» внедрения изменений. Цель – исследовать текущую ситуацию, сколько времени каждому оператору, чтобы взять заготовку, обработать ее на станке и отнести на стеллаж.
Замеры делаются по функциям и ролям как можно детальнее минимум 3 дня. Если это офис – то, как далеко ходит бухгалтер до принтера. Например, принтер расположен в дальнем углу от рабочего стола на расстоянии 15 м, печатает чаще всех – более 20 раз за день. Вот и получается, что бухгалтер наматывает 600 м впустую.
Встречались случаи в практике, когда принтер находился в другом кабинете, у руководителя. Руководитель печатает раз в 3 дня, а сотрудник – 18 раз на день. Мало того, что метры наматывает, но и еще беспрерывно отрывает руководителя (как стать эффективным руководителем можно почитать отдельно).
Поэтому цель данного этапа — рациональное расположение не только мелких инструментов, но и предметов мебели или станков. Расположение по потоку движения, как удобнее и быстрее выполнять свою работу.
После замеров и анализа деятельности, необходимо совместное обсуждение нового расположения. Подчеркну, совместного, это
genuspeha.ru
5S на транспорте — 1 шаг 5С и введение
Рис. 1. Лестница создания эффективного рабочего места.
Система устанавливает пять шагов, выполнение которых направлено на создание условий для стабильного оптимального выполнения операций, поддержание порядка, чистоты, аккуратности, экономии времени и энергии для повышения производительности, предотвращения несчастных случаев, снижения загрязнения окружающей среды.
Таблица 1
Основные принципы системы 5С
Принцип |
Содержание работы |
1. Сортировка: оставьте только нужное (ККЯ) |
Все предметы разделяются на три категории: нужные, не нужные срочно и ненужные. Нужные сохраняются на рабочем месте. Не нужные срочно располагаются на определенном удалении от рабочего места или хранятся централизованно Ненужные удаляются. |
2. Свои места для всего: каждой вещи свое место |
По отношению к нужным предметам и предметам не нужным срочно вырабатываются и реализуются решения, которые обеспечивают: ·быстроту, легкость и безопасность доступа к ним; ·визуализацию способа размещения и контроля наличия, отсутствия или местонахождения нужного предмета; ·свободу перемещения предметов и эстетичность рабочего места (автомобиля). |
3. Содержание в чистоте: рабочее место в исправном, подготовленном к работе состоянии |
Тщательная уборка и очистка рабочего места (автомобиля) и оборудования. Фиксация и устранение неисправностей. Выявление источников загрязнения, труднодоступных и проблемных мест. Выработка и реализация мер по уборке труднодоступных мест, ликвидации источников проблем и загрязнений. Выработка правил проведения уборки-проверки, чистки оборудования, смазки. |
4. Стандартизация процедур поддержания чистоты и порядка |
Фиксация в письменном виде правил и стандартов выполнения рабочих операций, направленных на: удаление ненужного, рациональное размещение предметов, уборку, смазку, проверку. |
5. Самодисциплина: стимулируйте поддержание порядка |
Закрепление сфер ответственности за каждым водителем (объекты внимания и основные обязанности по их поддержанию в нормальном состоянии). Применение эффективных методов контроля – чек-лист. |
В целом применение системы 5С позволяет создавать эффективные рабочие места, что в дальнейшем дает экономию средств, улучшает качество, поднимает эффективность перевозки товара, повышает уровень производительности и безопасности труда.
Система 5С направлена на следующие объекты:
— Внешний вид водителя;
— Рабочие зоны:
— Салон автомобиля
— Кузов автомобиля
— Внешнее состояние автомобиля
— Техническое состояние автомобиля
— Предметы у водителя и в зоне:
— Спецодежда, документы, электронные устройства.
— Предметы и оборудование, необходимые для выполнения работы (ККМ, сейф, погрузочно-разгрузочное оборудование, стяжные ремни, противооткатное устройство)
— Предметы, необходимые по правилам дорожного движения (аптечка, огнетушитель, знак аварийной остановки и т.д.)
— Средства для ремонта автомобиля (запасное колесо, домкрат, балонный ключ)
4. ОРГАНИЗАЦИЯ РАБОТ ПО ВНЕДРЕНИЮ СИСТЕМЫ 5С
4.1 Перед началом работы необходимо определить:
— Цель работы
— Руководителя работ
— Состав рабочих групп
— План-график проведения встреч рабочих групп
4.2 Ответственность за внедрение системы 5С в филиале возлагается на Заместителя директора филиала. Ответственность за проведение и поддержание системы 5С на грузовых автомобилях возлагается на сотрудника, ответственного за выпуск автомобиля на линию.
4.3 Рекомендуемый состав рабочей группы:
— Заместитель директора филиала;
— сотрудник, ответственный за выпуск автомобиля на линию;
— водитель/водители.
Примечание: состав группы может быть иным, в зависимости от организационной структуры подразделения.
5. ШАГ №1 СИСТЕМЫ 5С: СОРТИРУЙТЕ: ОСТАВЬТЕ ТОЛЬКО НУЖНОЕ
5.1. Цель первого этапа 1С – определить необходимые для рабочей деятельности предметы, освободить рабочее пространство от ненужных предметов, создать предпосылки для организации визуального управления и стабилизации процесса.
5.2. В случае, если чистота и санитарное состояние автомобиля находятся на невысоком уровне, целесообразно начать с генеральной уборки, которая позволит быстро освободиться от существующей части грязи и мусора, неприятных запахов. Кроме того, самому водителю необходимо привести себя в порядок и свой внешний вид. Затем приступать к реализации первого шага системы 5С.
Схема проведения 1С представлена в таб. 2.
Таблица 2
№ этапа |
Этап |
Название этапа |
1.1 |
Подготовительный |
Определение графика проведения Сортировки |
Определение перечня работ |
||
1.2 |
Определение критериев необходимости предметов в автомобиле и у водителя |
|
1.3 |
Фотографирование водителя и автомобиля |
|
2.1 |
Реализация |
Идентификация предметов у водителя и в автомобиле |
2.2 |
Оценка степени необходимости каждого предмета, принятие решений |
|
2.3 |
Документирование результатов 1С, фиксирование списка необходимых предметов в контрольный листок |
|
2.4 |
Удаление предметов, по которым принято соответствующее решение, из автомобиля и у водителя |
|
Перемещение предметов, по которым принято соответствующее решение |
5.3.1. Подготовительный этап.
5.3.1.1. Рабочая группа проводит организационное совещание, на котором:
— разрабатывает график проведения 1С;
— участниками рабочей группы изучаются теоретические и методические материалы. При необходимости для проведения обучения руководитель группы приглашает кайдзен-менеджера если таковой сотрудник имеется в компании или на предприятии.
— Определяются способы и порядок удаления предметов.
Примечание: рекомендуемые способы удаления предметов:
• Выбросить (самое последнее)
• Передать другим водителям
• Продать
• Передать другому подразделению
Также рабочая группа перед началом шага 1С разъясняет водителям цели и задачи 1С и системы 5С в целом.
5.3.1.2. Рабочая группа определяет критерии необходимости предметов в автомобиле и у водителя. Рекомендуется за основу взять следующие три критерия:
— Необходимость предмета при выполнении текущей деятельности. Это могут быть как предметы, используемые непосредственно в работе водителя (стяжные ремни, документы на груз, перчатки, ручка, мобильный телефон и т.д.), так и предметы первой необходимости (аптечка, огнетушитель, знак аварийной остановки). Если предмет не нужен, он должен быть удален из рабочей зоны (кабина или кузов) и удален у водителя;
— Частота использования. Если предметом пользуются редко, то его можно хранить вне рабочего места;
— Количество предметов, необходимых для текущей деятельности. Если нужно ограниченное количество предметов, излишки можно удалить или хранить вне рабочего места. К примеру, если положено 4 стяжных ремня, то должно быть 4 (максимум 6 – на случай дополнительного крепежа, поломки или повреждения) стяжных ремня. Также и с пишущей ручкой. Нет необходимости хранить несколько ручек в разных частях салона (двери, бардачок, панель приборов, подлокотник и др.). Достаточно 1-2 ручек для оформления документов.
5.3.1.3. Рабочая группа фотографирует текущую ситуацию в автомобиле и самого водителя. Фотографирование автомобиля должно проходить со всех сторон, включая рабочие зоны (салон и кузов). Также фотографируется водитель спереди и сзади во весь рост. Фотографии сохранены в папку с указанием даты фотосъемки.
5.3.2. Этап реализации
5.3.2.1. Рабочая группа проводит идентификацию предметов в автомобиле и у водителя, а также определяет степень необходимости этих предметов и в соответствии с этим принимает решение об их дальнейшей судьбе:
— оставить предмет там, где он находится
— изменить количество
— переместить предмет на новое место в пределах автомобиля;
— утилизировать;
В результате должен быть сформирован список необходимых предметов всех рабочих зон и у водителя, который используется для формирования Контрольного листка (см. п. 5.4.3)
5.3.2.2. Удаление ненужных предметов.
— Выявленные лишние предметы должны быть удалены из автомобиля сразу же после принятия решения о способе удаления.
Примечание: Возможные рекомендуемые способы удаления предметов:
• Выбросить – для выявленных лишних предметов, не представляющих ценности.
• Передать другим подразделениям или водителям – для выявленных лишних предметов, представляющих ценность, и необходимых на других участках.
• Продать – для выявленных лишних предметов, представляющих ценность, но не нужных для выполнения рабочих операций.
5.3.3. Контроль эффективности первого шага системы 5С
Контроль эффективности внедрения первого шага системы 5С осуществляется при помощи «Контрольного листа по проверке эффективности внедрения первого шага системы 5С». Контрольный лист 1-го уровня (аудит выполняется самим водителем) должен храниться в салоне автомобиля в лотке или папке.
Эффективность внедрения первого шага оценивается по автомобилю и водителю в целом. Наличие правил отнесения предметов к нужным, кол-во предметов и место их нахождения.
iambuilding.ru
Бережливое производство и 5С в ОАО РЖД
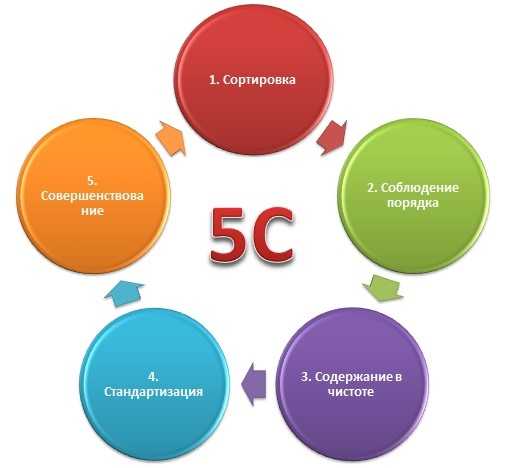
5С – это методика особой организации рабочего места с целью создания наиболее оптимальных условий для выполнения рабочих операций, поддержания порядка на рабочем месте, чистоты, аккуратности, экономии времени и энергии. 5С это один из важнейших инструментом бережливого производства применяемых в ОАО РЖД.
Чистота и порядок на рабочем месте сотрудника, а не «упорядоченный хаос», вот залог всех улучшений, повышения качества и производительности в промышленном производстве и других отраслях. Только в хорошо организованной среде могут производиться бездефектные, соответствующие требованиям клиентов товары и услуги и достигаться соответствующая наивысшим требованиям результативность применяемых процессов.
Основными предпосылками для получения этого является методика 5С, или 5 шагов.
Шаг 1 – Сортировка, удаление ненужного.
На рабочем месте все предметы разделяются на необходимые и ненужные. Производится удаление ненужных предметов. Эти действия на рабочем месте приводят к улучшению культуры и безопасности труда. Все сотрудники вовлекаются в отсортировку и определение предметов, которые должны быть:
- немедленно удалены и утилизированы;
- перенесены в место для хранения;
- оставлены, как необходимые и для выполнения работы.
Шаг 2 – Самоорганизация, соблюдение порядка, определение для каждой вещи своего места.
Навести порядок с необходимыми предметами. Необходимые предметы располагают на определенные места так, чтобы они были легко доступными для каждого, кто пользуется ими! Следует также промаркировать их для быстрого поиска.
Шаг 3 – Соблюдение чистоты, систематическая уборка.
Создается система, в которой ничего больше не загрязняется. Убедиться, что всё находится на своих местах. Рабочие зоны для рабочих мест должны быть разграничены и обозначены. Регулярно и часто убирать, чтобы в случае, когда вам что-нибудь понадобится, оно находилось на месте и в рабочем состоянии. Тщательная уборка оборудования обеспечивает предотвращение и идентификацию возможных проблем в работе.
Шаг 4 – «Стандартизировать» процесс.
Поддерживать порядок и чистоту посредством регулярного выполнения первых трех шагов. Самые эффективные решения, найденные в ходе реализации первых трех шагов необходимо закрепить письменно, чтобы стать наглядными и легко запоминающимися. Разработать стандарты документов, приемов работы, обслуживания оборудования, техники безопасности с использованием визуального контроля.
Шаг 5 – Совершенствование порядка и дисциплина.
Для поддержания рабочего места в нормальном состоянии выполнять работу дисциплинированно, в соответствии с установленными стандартами. Осознание системы 5С как общепринятой повседневной деятельности и ее совершенствование. Визуализировать действия по улучшению: выявлять улучшения в оборудовании; записывать предложения для улучшений; внедрять новые улучшенные стандарты.
Еще по теме:
cssrzd.ru
Что такое 5S? Система 5S. Система 5с
14 Октябрь 2011 Евгений Неделин Просмотров:Что такое система 5S
Система 5S – это система организации рабочего места, которая позволяет значительно повысить эффективность и управляемость операционной зоны, улучшить корпоративную культуру, повысить производительность труда и сохранить время. Это первый шаг на пути к созданию бережливого предприятия и применению других инструментов системы менеджмента компании Toyota.
Краткая история системы 5S
В Японии системный подход к организации, наведению порядка и уборке рабочего места возник в послевоенный период, точнее, к середине 50-х годов ХХ века. В то время японские предприятия были вынуждены работать в условиях дефицита ресурсов. Поэтому они разработали для своего производства метод, при котором учитывалось все и не было места никаким потерям.
Первоначально в японской системе было только 4 действия. Слова, обозначающие эти действия, в японском языке начинаются с буквы «S»:
- Seiri (整理)– Sorting – сортировка.
- Seiton (整頓) – Straighten or Set in Order –рациональноерасположение.
- Seiso (清掃) – Sweeping – уборка.
- Seiketsu (清潔) – Standardizing – стандартизация работ.
Позже добавилось пятое действие, его назвали Shitsuke (躾) – Sustaining – поддержание достигнутого и совершенствование, и оно завершило цепочку элементов, которые теперь известны как 5S.
Сейчас система 5S обладает фундаментальной мощью для того, чтобы изменять рабочие места и вовлекать в процесс улучшений всех работников.
В систему 5s входят пять действий:
1) Сортировка – означает, что вы высвобождаете рабочее место от всего, что не понадобиться при выполнении текущих производственных операций.
Рабочие и руководители часто не имеют привычки избавляться от предметов, которые больше не нужны для работы, сохраняя их поблизости «на всякий пожарный случай». Обычно это приводит к недопустимому беспорядку или к созданию препятствий для перемещения в рабочей зоне. Удаление ненужных предметов и наведение порядка на рабочем месте улучшает культуру и безопасность труда. Чтобы более наглядно продемонстрировать, сколько лишнего скопилось на рабочем месте, можно на каждый предмет-кандидат на удаление из рабочей зоны повесить красный ярлык (флажок).
Все сотрудники вовлекаются в сортировку и выявление предметов, которые:
- должны быть немедленно вынесены, выброшены, утилизированы;
- должны быть перемещены в более подходящее место для хранения;
- должны быть оставлены и для них должны быть созданы и обозначены свои места.
Необходимо чётко обозначить «зону красных ярлыков» предметов с красными флажками и тщательно её контролировать. Предметы, остающиеся нетронутыми свыше 30 дней, подлежат переработке, продаже или удалению.
2) Рациональное расположение – означает определить и обозначить «дом» для каждого предмета, необходимого в рабочей зоне. Иначе, если, например, производство организовано по сменам, рабочие разных смен будут класть инструменты, документацию и комплектующие в разные места. В целях рационализации процессов и сокращения производственного цикла крайне важно всегда оставлять нужные предметы в одних и тех же отведённых для них местах. Это ключевое условие минимизации затрат времени на непродуктивные поиски.
3) Уборка (содержание в чистоте) – значит обеспечить оборудованию и рабочему месту опрятность, достаточную для проведения контроля, и постоянно поддерживать её.
Уборка в начале и/или в конце каждой смены обеспечивает немедленное определение потенциальных проблем, которые могут приостановить работу или даже привести к остановке всего участка, цеха или завода.
4) Стандартизация – это метод, при помощи которого можно добиться стабильности при выполнении процедур первых трех этапов 5S – значит разработать такой контрольный лист, который всем понятен и прост в использовании. Продумать необходимые стандарты чистоты оборудования и рабочих мест, и каждый в организации должен знать, как это важно для общего успеха.
5) Совершенствование – означает то, чтобы выполнение установленных процедур превратилось в привычку
Мероприятия, лежащие в основе 5S (сортировка, рациональное расположение, уборка, стандартизация и совершенствование), абсолютно логичны. Они представляют собой базовые правила управления любым продуктивно работающим отделом. Однако именно системный подход, который система 5S применяет к этим мероприятиям, и делает ее уникальной.
См. также:
Что такое 5S. Система 5S. Система 5с
Рейтинг публикации:
Загрузка…Поделиться в соцсетях:
Метки: бережливое производствоwww.training-partner.ru
5C на складе — Шаг 1
Начало
В данной методической рекомендации дается определение системе 5С, устанавливаются основные принципы, порядок проведения, контроля и поддержания системы 5С на складе.2.Термины и определения
В последующих статьях по данной методике будем встречать различные термины и определения, что бы сразу исключить двойное толкование, давайте разберем все термины:Визуальное управление – любое средство, информирующее о том, что должно происходить в зоне в нормальном состоянии (как выполняется работа, стандартные процедуры выполнения работы, наличие и местонахождение предметов и т.д.).
Зона карантина – обозначенное и идентифицированное место на территории предприятия, предназначенное для временного хранения предметов, помеченных красными ярлыками и ожидающих дальнейшего оценивания. Эта зона обеспечивает необходимую подстраховку от поспешного принятия решений по поводу ненужности того или иного предмета.
Кампания красных ярлыков (ККЯ) – это метод, который позволяет определить потенциально ненужные предметы, оценить степень их полезности и в соответствии с этим принять решение об их дальнейшем местонахождении. На предметы, нуждающиеся в оценке степени их необходимости, наклеиваются красные ярлыки.
Красный ярлык – бланк красного цвета с необходимой информацией. Служит инструментом визуального выделения и идентификации ненужных предметов.
Рабочая группа – временная группа, состоящая из специалистов и руководителей подразделения, целью деятельности которой является поиск и принятие решения по заданной проблеме.
Рабочее место – зона трудовой деятельности человека или часть пространства, которая оснащена необходимым оборудованием, инструментами и материалами для выполнения предусмотренных должностными инструкциями работ.
Камишибаи (яп. Бумажная игра) – Изначально способ рассказать историю в картинках в японском театре. Здесь – инструмент визуального контроля выполнения нескольких видов работ. Серия карточек расположена в последовательности выполнения работы. Карточки двусторонние (красные и зеленые), переворачиваются с красной стороны на зеленую по факту выполнения задания.
FIFO — (англ. First In, First Out — «первым пришёл — первым ушёл») — способ организации и манипулирования предметами относительно времени и приоритетов.. Товар поступивший на склад первым, отгружается со склада в первую очередь.
LIFO — (англ. Last In, First Out, «последним пришёл — первым ушёл») — способ организации и манипулирования предметами относительно времени и приоритетов. В структурированном линейном списке, организованном по принципу LIFO, грузы могут добавляться и выбираться только с одного конца, называемого «вершиной списка». Структура LIFO может быть проиллюстрирована на примере стопки тарелок: чтобы взять вторую сверху, нужно снять верхнюю, а чтобы снять последнюю, нужно снять все, лежащие выше.
FEFO — (англ. First Expire, First Out — «первый истекает — первый выходит») При использовании данного метода при ротации грузов учитывается остаточный срок годности предмета (Use By Date, UBD; Expiration date). Предметы с минимальным остаточным сроком годности отгружаются в первую очередь.
FPFO — (англ. First Product First Out — первый произведен — первый выходит) При использовании данного метода при ротации предметов учитывается дата выпуска продукции. Более старая продукция отгружается в первую очередь. Использование данного метода характерно для производственных складов.
3.Общая часть
Система 5С представляет собой совокупность организационно- технических мероприятий по рациональной организации рабочих мест, обеспечивающей базовую стабилизацию выполнения процесса, безопасность людей, рост производительности труда, повышение качества продукции, повышение культуры производства.
Система 5С – один из инструментов базовой стабилизации, направленных на реализацию принципа «точно вовремя»
Система получила название от первых букв пяти русских слов:
— Сортировка
— Свои места для всего
— Содержание в чистоте
— Стандартизация
— Самодисциплина/совершенствование
Рисунок 1.
Рис. 1. Лестница создания эффективного рабочего места.
Система устанавливает пять шагов, выполнение которых направлено на создание условий для стабильного оптимального выполнения операций, поддержание порядка, чистоты, аккуратности, экономии времени и энергии для повышения производительности, предотвращения несчастных случаев, снижения загрязнения окружающей среды.
Основные принципы системы 5С
Принцип |
Содержание работы |
1. Сортировка: оставьте только нужное (ККЯ) |
Все предметы разделяются на три категории: нужные, не нужные строчно и ненужные. Нужные сохраняются на рабочем месте. Не нужные срочно располагаются на определенном удалении от рабочего места или хранятся централизованно Ненужные удаляются. |
2. Свои места для всего: каждой вещи свое место |
По отношению к нужным предметам и предметам не нужным срочно, вырабатываются и реализуются решения, которые обеспечивают: быстроту, легкость и безопасность доступа к ним; визуализацию способа хранения и контроля наличия, отсутствия или местонахождения нужного предмета; свободу перемещения предметов и эстетичность производственной среды. |
3. Содержание в чистоте: рабочее место в исправном, подготовленном к работе состоянии |
Тщательная уборка и очистка оборудования, фиксация и устранение неисправностей. Выявление источников загрязнения, труднодоступных и проблемных мест. Выработка и реализация мер по уборке труднодоступных мест, ликвидации источников проблем и загрязнений. Выработка правил проведения уборки-проверки, чистки оборудования, смазки. |
4. Стандартизация процедур поддержания чистоты и порядка |
Фиксация в письменном виде правил: удаления ненужного, рационального размещения предметов, уборки, смазки, проверки.
|
5. Самодисциплина/ Совершенствование стимулируйте поддержание порядка |
Закрепление сфер ответственности за каждым работником (объекты внимания и основные обязанности по их поддержанию в нормальном состоянии). Выработка у персонала правильных привычек, закрепление навыков соблюдения правил. Применение эффективных методов контроля. |
В целом применение системы 5С позволяет создавать эффективные рабочие места, что в дальнейшем дает экономию средств, улучшает качество, поднимает эффективность производства, повышает уровень производительности и безопасности труда.
Система 5С направлена на следующие объекты:
А) Рабочие зоны
— Полы
— Проходы
— Стены
Б) Предметы в зоне:
— Товары, запасы, изделия.
— Оборудование – стеллажи, тележки, инструменты, рабочие столы, компьютеры, шкафы и т.д.
4. Организация работ по внедрению системы
4.1 Перед началом работы необходимо определить:
— Цель работы
— Руководителя работ
— Состав рабочих групп
— План-график проведения встреч рабочих групп
— Рабочие зоны для внедрения системы 5С и очередность внедрения в разных зонах.
Примечание: в одной зоне должны быть одинаковые процессы обработки и одинаковое используемое оборудование. В противном случае это разные зоны. (напр. длинномерный товар, краска и т.п.) Предпочтительно делать разбивку на небольшие зоны. В случае нахождения в зоне большого количества наименований предметов (больше 20) рекомендуется разбить зону на несколько меньших. Все зоны должны быть обозначены на схематичной планировке с указанием ответственного лица за внедрение системы 5С.
4.2 Ответственность за внедрение системы 5С возлагается на высшего руководителя склада где производится внедрение. Ответственность за проведение и поддержание системы 5С на своем участке возлагается на руководителя участка вне зависимости от количества подчиненных данного руководителя.
4.3 Рекомендуемый состав рабочей группы:
— Руководитель подразделения – руководитель группы 5С
— Сотрудники подразделения – участники группы 5С (3-5 чел.).
— Сотрудники других подразделений — участники группы 5С (1-3 чел.).
Примечание: состав группы может быть иным, в зависимости от организационной структуры подразделения
4.4 Рабочих групп может быть несколько в зависимости от масштаба и возможностей предприятия.
Участники рабочей группы должны пройти инструктаж по соблюдению правил охраны труда и техники безопасности при проведении работ по системе 5С.
5. ШАГ 1 Системы 5С: Сортируйте: Оставьте только нужное (Кампания Красных Ярлыков)
5.1 Цель первого этапа 1С – определить необходимые для рабочей деятельности предметы, освободить рабочее пространство от ненужных предметов, создать предпосылки для организации визуального управления и стабилизации процесса.
5.2 В случае, если производственная культура, чистота и санитарное состояние зоны находятся на невысоком уровне, целесообразно начать с генеральной уборки, которая позволит быстро освободиться от существующей части грязи и мусора. А затем приступать к реализации первого шага системы 5С.
5.3 Порядок проведения 1С
Схема проведения 1С представлена в таб. 1.
№ этапа |
Этап |
Название этапа |
1.1. |
Подготовительный |
Определение графика проведения Сортировки |
Определение перечня работ |
||
Распределение ролей и ответственности между участниками группы |
||
1.2 |
Выбор и организация зоны «Карантина» |
|
1.3 |
Определение критериев необходимости предметов в зоне |
|
1.4 |
Изготовление красных ярлыков |
|
1.5 |
Фотографирование состояния зоны и предметов в ней |
|
2.1 |
Реализация |
Идентификация предметов в зоне |
Прикрепление красных ярлыков к предметам в зоне |
||
2.2 |
Оценивание степени необходимости каждого предмета в зоне, принятие решений |
|
2.3 |
Запись в журнале регистрации красных ярлыков |
|
Документирование результатов 1С, Фиксирование списка необходимых предметов в контрольный листок |
||
2.4 |
Удаление предметов, по которым принято соответствующее решение, из рабочей зоны |
|
|
Перемещение предметов, по которым принято соответствующее решение, в карантин |
5.3.1 Подготовительный этап.
5.3.1.1 Рабочая группа проводит организационное совещание, на котором:
— разрабатывается график проведения 1С
— распределяются роли и ответственность между участниками группы (Пример см. Приложение 1).
— участниками рабочей группы изучаются теоретические и методические материалы. При необходимости для проведения обучения руководитель группы приглашает кайдзен-менеджера.
— Определяются способы и порядок удаления предметов.
Примечание: рекомендуемые способы удаления предметов:
• Выбросить
• Передать другим подразделениям
• Продать
• Переместить в зону карантина
Также рабочая группа перед началом шага 1С разъясняет сотрудникам участка цели и задачи 1С и системы 5С в целом.
5.3.1.2 Для реализации 1С в при необходимости организуется «Зона карантина».
«Зона карантина» представляет собой временное место хранения ненужных предметов, ожидающих решения о целесообразности их нахождения на территории данного участка, обозначенное информационной табличкой «Зона карантина».
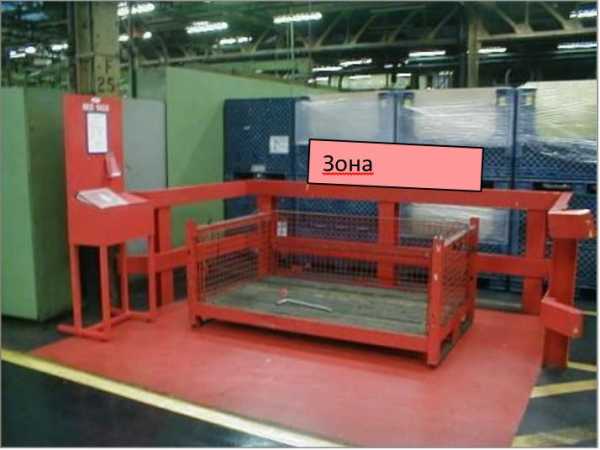
Рис. 2. Пример «Зоны карантина»
В случае принятия решения об удалении из рабочей зоны крупногабаритного предмета (например, стеллажа), допускается его оставить на месте, с прикрепленным «красным ярлыком» и надписью «временно не используется». Это означает, что оборудование будет удалено позже.
5.3.1.3 Рабочая группа определяет критерии необходимости предметов в зоне. Рекомендуется за основу взять следующие три критерия:
— Необходимость предмета при выполнении текущей деятельности. Если предмет не нужен, он должен быть удален из рабочей зоны;
— Частота использования. Если предметом пользуются редко, то его можно хранить вне рабочего места;
— Количество предметов, необходимых для текущей деятельности. Если нужно ограниченное количество предметов, излишки можно удалить или хранить вне рабочего места.
5.3.1.4 Рабочая группа готовит необходимые технические средства, инвентарь, документы: бланки «Красный ярлык» (Приложение 2 и Приложение 3) – не менее 4 штук на 1 участника рабочей группы, журнал для регистрации красных ярлыков (Приложение 4 и Приложение 5) и др.
5.3.1.5 Рабочая группа фотографирует текущую ситуацию в зоне, определяя и фиксируя точки и углы фотосъемки. Фотографирование должно проходить от периметра к центру, во время работы. Фотографии сохранены в папку в указанием даты фотосъемки.
5.3.2 Этап реализации
5.3.2.1 Рабочая группа проводит идентификацию предметов в зоне, а также определяет степень необходимости этих предметов и в соответствии с этим принимает решение об их дальнейшей судьбе:
— оставить предмет там, где он находится
— изменить количество
— переместить предмет на новое место в рабочей зоне
— переместить в «Зону карантина»;
— утилизировать;
5.3.2.2 В случае сомнений по поводу необходимости предмета, к нему прикрепляется «красный ярлык». При идентификации предмета красным ярлыком необходимо следовать правилу «Один предмет – один ярлык». Идентификация нескольких предметов одним красным ярлыком возможна, если предметы одинаковы или хранятся в некоторой общей таре. В соответствии с оценкой принимается решение о дальнейшей судьбе предмета
5.3.2.3 Рабочая группа регистрирует результаты кампании красных ярлыков в «журнале регистрации красных ярлыков».
Все красные ярлыки, которыми помечены предметы, подлежат обязательной регистрации. Красные ярлыки регистрируются в «Журнале регистрации красных ярлыков» (Приложение 4), который хранится в «Зоне карантина». Требования к заполнению «Журнала» приведено в Приложении 5.
Также в результате должен быть сформирован список необходимых предметов зоны, который используется для формирования Контрольного листка (см. п. 5.4.3)
5.3.2.4 Удаление ненужных предметов.
— Выявленные лишние предметы должны быть удалены из зоны в течение трех рабочих дней после принятия решения о способе удаления.
Примечание: Возможные рекомендуемые способы удаления предметов:
• Выбросить – для выявленных лишних предметов, не представляющих ценности
• Передать другим подразделениям – для выявленных лишних предметов, представляющих ценность, и необходимых на других участках
• Продать – для выявленных лишних предметов, представляющих ценность, но не нужных на предприятии
• Переместить в зону карантина – для выявленных лишних предметов, представляющих ценность, решение по которым будет принято позднее.
— Факт удаления предмета, идентифицированного красным ярлыком, в том числе в «Зону карантина», руководитель рабочей группы отмечает в соответствующих графах «Журнала регистрации красных ярлыков».
— В «Зону карантина» помещаются предметы, ожидающие дальнейшего оценивания. Срок хранения предметов в «Зоне карантина» определяется рабочей группы, но не может быть более 2-х месяцев.
5.4.3 Контроль эффективности первого шага системы 5С
Контроль эффективности внедрения первого шага системы 5С осуществляется при помощи «Контрольного листа по проверке эффективности внедрения первого шага системы 5С» (Приложение 6).
Состояние «Зоны карантина» оценивается с точки зрения её заполненности. В идеальном случае она должна быть пустой или ликвидирована. Допускается в ней наличие предметов, требующих дальнейшего оценки, но с прикрепленным красным ярлыком (с указанием срока удаления) и надписью.
Эффективность внедрения первого шага оценивается по каждой зоне отдельно.
В следующей статье, ШАГ 2. Все материалы в электронном виде, будут приложены к статье с последней частью!
iambuilding.ru
Добавить комментарий
Комментарий добавить легко